Hobbywing XRotor micro 20A BLHeli Handleiding
Hobbywing
Radiografisch bestuurbaar speelgoed
XRotor micro 20A BLHeli
Lees hieronder de 📖 handleiding in het Nederlandse voor Hobbywing XRotor micro 20A BLHeli (1 pagina's) in de categorie Radiografisch bestuurbaar speelgoed. Deze handleiding was nuttig voor 50 personen en werd door 2 gebruikers gemiddeld met 4.5 sterren beoordeeld
Pagina 1/1
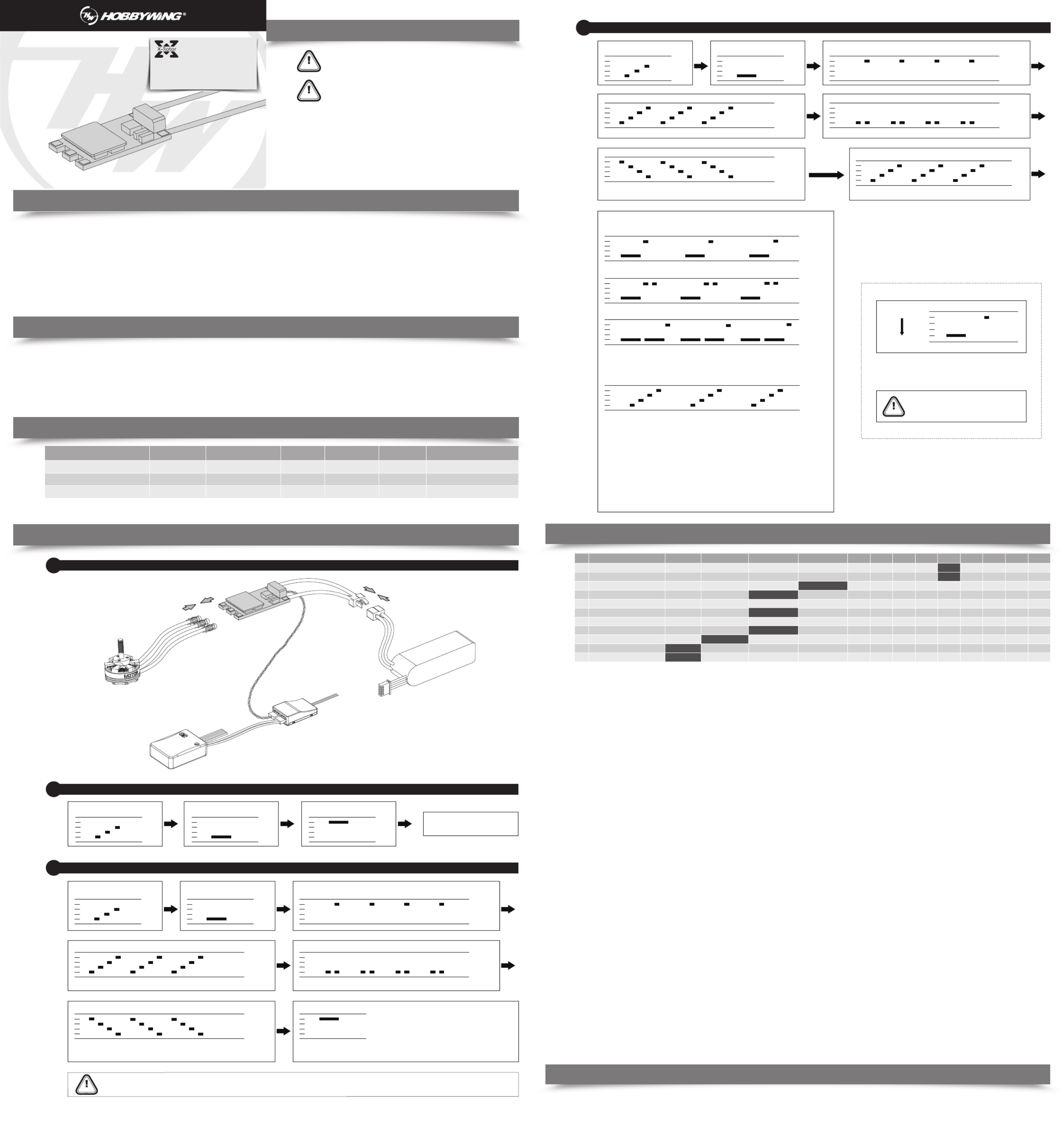
07
Others
06
Programmable Items
• F396 chip for great performance , 48MHz .
• BLHeli open-source program implemented in the ESC supports all BLHeli functions like ESC programming and firmware upgrade via the throttle control signal cable.
• Small size combined with light weight for easy installation.
• Compatible with “Regular” signal-receiving mode and “OneShot” signal-receiving mode (that is the ESC can receive fixed throttle signals range from 125µs~250µs).
• The twisted-pair design of the throttle signal cable effectively reduces the crosstalk produced in signal transmission and makes flight more stable.
• Compatible with various flight-controllers and supports a signal frequency of up to 500Hz in “Regular”signal-receiving mode.
Thank you for purchasing this HOBBYWING product! Brushless power
systems can be very dangerous. Any improper use may cause personal injury
and damage to the product and related devices. We strongly recommend
reading through this user manual before use. Because we have no control
over the use, installation, or maintenance of this product, no liability may be
assumed for any damage or losses resulting from the use of the product. We
do not assume responsibility for any losses caused by unauthorized
modifications to our product.
We, HOBBYWING, are only responsible for our product cost and nothing else
as result of using our product.
• Read through the manuals of all power devices and aircraft and ensure the power configuration is rational before using this unit, as incorrect configuration may cause the ESC to overload
and be damaged.
• Ensure all wires and connections must be well insulated before connecting the ESC to related devices, as short circuit will damage your ESC. And ensure all devices are well connected,
(please use a soldering iron with enough power to solder all input/output wires and connectors if necessary,) as poor connection may cause your aircraft to lose control or other
unpredictable issues such as damage to the device.
• Do not use this unit in the extremely hot weather or continue to use it when it gets really hot (around 105 /221 ). Because high temperature will cause the ESC to work abnormally or ℃ ℉
even damage it.
• Users must always disconnect the batteries after use as the current on the ESC is consuming continuously if it`s connected to the batteries (even if the ESC is tur ned off). The battery will
completely be discharged and may result in damage to the battery or ESC when it is connected for a long period of time. This will not be covered under warranty.
IMP OR T ANT
Throttle Range Calibration
3
Once
1. Power up:
Once
2. Throttle up detected
(arming sequence start):
Once
7. Throttle calibration is finished:
While
measuring
3. Zero throttle detected (arming sequence end):
Once
1. Power up:
Once
2. Throttle up detected
(arming sequence start):
While
measuring
3. Zero throttle detected (arming sequence end):
While
measuring
5. When throttle is below midstick (measuring min throttle):
Once
4. If throttle is above midstick for 3 seconds:
This beep sequence indicates that max throttle has been stored
Attention!
. This operation is only applicable to
code revision 14.4 and later.
. There is no such beep sequence for
prior code revisions. Users need to
disconnect the battery from the ESC,
and then reconnect it to the ESC.
Once
6. If throttle is below midstick for 3 seconds:
This beep sequence indicates that min throttle has been stored This beep sequence indicates the throttle
calibration is finished, and the ESC is ready to go.
This is an extremely powerful brushless motor system. We strongly recommend removing your propellers for your own safety and the safety of those around you
before performing calibration and programming functions with this system.
ESC Programming
4
While
measuring
5. When throttle is below midstick (measuring min throttle):
Once
4. If throttle is above midstick for 3 seconds:
This beep sequence indicates that max throttle has been stored
Once
Once
7. Full throttle detected after the throttle stick is moved to the top position:
This beep sequence indicates that programming mode is entered.
Enter
programming
mode
Once
6. If throttle is below midstick for 3 seconds:
This beep sequence indicates that min throttle has been stored
Once
8. Beeps - Programming mode"
Function 1, parameter value 1
Once
Function 1, parameter value 2
Once
Function 2, parameter value 1
Parameter value stored
...etc...
If the throttle stick is moved to zero during one of the above sequences,
the parameter value of that function is selected and stored. And you will hear this sound:
The ESC then resets itself.
IMP OR T ANT
Illustration:
Long beep
Short beep
Maximum Volume
Minimum Volume
It will be more convenient if users adjust
parameters via BLHeli Suite (configuration
software).
Model
XRotor micro 20A BLHeli
XRotor micro 30A BLHeli
XRotor micro 35A BLHeli
Cont. Current
20A
30A
35A
Peak Current (10sec)
30A
40A
50A
BEC
No
No
No
LiPo
2-4S
2-4S
3-6S
Weight
6.8g
6.8g
9.5g
Size
24.0 x 13.9 x 5.5 mm
24.0 x 13.9 x 5.5 mm
36.5 x 16.7 x 5.5 mm
Motor Wiring
1
Normal Start-up Process
2
Once
1. Power up:
Once
2. Throttle up detected
(arming sequence start):
Once
3. Zero throttle detected
(arming sequence end):
4. After this, the motor will run.
OK
UBEC
Motor
Receiver
Battery
Electronic
Speed
Controller
(Those “gray background and black text” options are the factory default settings.)
*: Only enabled for some ESCs. From code rev 14.4, damped light is default on the ESCs that support it. For prior code revisions, high is default.
**: Default startup power varies by ESC. Generally the default power is lower for larger ESCs.
If for some reason there is an error in the eeprom/flash write operation (e.g. due to loss of power or low voltage), defaults will be loaded.
1. Closed Loop P Gain: it sets the proportional gain for the rpm control loop.
This setting controls the gain from speed error to motor power.
2. Closed Loop I Gain: it sets the integral gain for the rpm control loop.
This setting controls the gain from integrated speed error (summed over time) to motor power.
3. Closed Loop Mode: it sets the range of speeds that the control loop can operate on.
• For the high range, throttle values from 0% to 100% linearly correspond to rpm targets from 0 to 200000 electrical rpm.
• For the middle range, throttle values from 0% to 100% linearly correspond to rpm targets from 0 to 100000 electrical rpm.
• For the low range, throttle values from 0% to 100% linearly correspond to rpm targets from 0 to 50000 electrical rpm.
When closed loop mode is set to Off, the control loop is disabled.
4. Multi Gain: it scales the power applied to the motor for a given input.
Note that this is only for PWM input, for PPM input it has no effect. Beware that a low multi gain will also limit the maximum power to the motor.
5. Startup Power: it is always done with the direct startup method, which runs the motor using back emf detection from the very start.
In this mode power is given by the throttle used, but limited to a maximum level. This maximum level can be controlled with the startup power parameters. Beware that setting startup
power too high can cause excessive loading on ESC or motor.
6. Commutation Timing: it can be adjusted in five steps.
Low is about 0°, mediumlow 8°, medium 15°, mediumhigh 23° and high 30°.
Typically a medium setting will work fine, but if the motor stutters it can be beneficial to change the timing.
7. PWM Frequency
High pwm frequency is around 20kHz, and low pwm frequency is around 8kHz.
Pwm damped light mode: it adds loss to the motor for faster retardation and it always uses high pwm frequency. It is only supported on some ESCs where fet switching is sufficiently fast.
8. PWM Dither: it’s a parameter that adds some variation to the motor pwm off cycle length. This can reduce problems (like throttle steps or vibration) in rpm regions where the pwm
frequency is equal to harmonics of the motor commutation frequency, and it can reduce the step to full throttle. It is primarily beneficial when running damped light mode, Dither is not
applied in closed loop mode.
9. Demag Compensation: it’s a feature to protect from motor stalls caused by long winding demagnetization time after commutation. The typical symptom is motor stop or stutter upo quick
throttle increase, particularly when running at a low rpm. As described earlier, setting high commutation timing normally helps, but at the cost of efficiency.
Generally, a higher value of the compensation parameter gives better protection.
If demag compensation is set too high, maximum power can be somewhat reduced.
10. Rotation Direction: it can be used to reverse motor rotation.
11. Input PWM Polarity: it can be used to inverse the throttle behavior and it’s intended to be used with receivers that provide negative pwm (at least some Walkeras do).
When using PPM input it must be set to positive.
Programming parameters that can only be accessed from configuration software (BLHeliSuite):
• Throttle minimum and maximum values for PPM input (will also be changed by doing a throttle calibration).
•
Throttle center value for bidirectional operation with PPM.
•
Beep strength, beacon strength and beacon delay.
•
Programming by TX. If disabled, the TX can not be used to change parameter values (default is enabled).
•
Thermal protection can be enabled or disabled (default is enabled).
•
(The motor power will be reduced to 75% when its temperature exceeds 140 ; the power will be reduced to 50% when the temperature is above 145 ; the power will be reduced to 25% ℃ ℃
when the temperature goes above 150 ; and the pwoer will be reduced to 0% if the temperature exceeds 155 .) ℃ ℃
•
PWM input can be enabled and disabled (default is disabled). If disabled, only 1-2ms PPM and 125-250µs OneShot125 are accepted as valid input singals. Set to disabled if using OneShot125
with looptimes below 1100.
•
Power limiting for low RPMs can be enabled or disabled (default is enabled). Disabling it can be necessary in order to achieve full power on some low KV motors running on a low supply
voltage. However, disabling it increases the risk of toasting motor or ESC.
Closed loop P gain
Closed loop I gain
Closed loop mode
Multi gain
Startup power**
Commutation timing
Pwm frequency
Pwm dither
Demag compensation
Rotation direction
Input pwm polarity
1
0.13
0.13
HiRange
0.75
0.031
Low
High
Off
Off
Normal
Positive
2
0.17
0.17
MidRange
0.88
0.047
MediumLow
Low
7
Low
Reversed
Negative
1
2
3
4
5
6
7
8
9
10
11
Function 3
0.25
0.25
LoRange
1.00
0.063
Medium
DampedLight*
15
High
Bidirectional
4
0.38
0.38
Off
1.12
0.094
MediumHigh
31
5
0.50
0.50
1.25
0.125
High
63
6
0.75
0.75
0.188
7
1.00
1.00
0.25
8
1.5
1.5
0.38
9
2.0
2.0
0.50
10
3.0
3.0
0.75
11
4.0
4.0
1.00
12
6.0
6.0
1.25
13
8.0
8.0
1.50
BLHeli official website https://github.com/bitdump/BLHeli:
BLHeliSuit download https://www.mediafire.com/folder/dx6kfaasyo24l/BLHeliSuite:
This BLHeli ESC Firmware XRotor 20A Multi BLHeli Rev 14.4: ( ) :
02
Warnings
03
Features
04
Specifications
05
User Guide
CA UT IONS
AT T ENT ION
01
Introduction
USER MANUAL
Multi-Rotor
XRotor micro 20A/30A/35A BLHeli
Brushless Electronic Speed Controller
If the throttle stick is moved below max (but not to zero), the current parameter will be
skipped, and programming will proceed to the next parameter. This way it is possible to
access the later parameters without going through all the beeps.
It is generally a good idea to go to full throttle again before selecting a parameter, to
make sure you have selected the right parameter.
Throttle is read in the 1 second pause between the function/parameter beeps.
If the throttle stick is never moved to zero, the ESC will load the defaults and then reset
itself after the last parameter value of the last function. This is a convenient way of
setting all parameters to defaults.
If power is disconnected during the programming sequence, then no changes are done to
the programmed values.
20161227
Product specificaties
Merk: | Hobbywing |
Categorie: | Radiografisch bestuurbaar speelgoed |
Model: | XRotor micro 20A BLHeli |
Kleur van het product: | Zwart |
Gewicht: | 7 g |
Breedte: | 24 mm |
Diepte: | 13.9 mm |
Hoogte: | 5.5 mm |
Correct gebruik: | Quadcopter |
Merkcompatibiliteit: | Hobbywing |
Type product: | Snelheidsregelaar |
Batterijtechnologie: | Lithium-Polymeer (LiPo) |
Stroom (max.): | 30 A |
AWG draad omvang: | 20 |
Heb je hulp nodig?
Als je hulp nodig hebt met Hobbywing XRotor micro 20A BLHeli stel dan hieronder een vraag en andere gebruikers zullen je antwoorden
Handleiding Radiografisch bestuurbaar speelgoed Hobbywing

29 Maart 2025

29 Maart 2025

27 Maart 2025

27 Maart 2025

27 Maart 2025

27 Maart 2025

27 Maart 2025

27 Maart 2025

27 Maart 2025

27 Maart 2025
Handleiding Radiografisch bestuurbaar speelgoed
- Radiografisch bestuurbaar speelgoed Absima
- Radiografisch bestuurbaar speelgoed ACME
- Radiografisch bestuurbaar speelgoed Amewi
- Radiografisch bestuurbaar speelgoed Blade
- Radiografisch bestuurbaar speelgoed DJI
- Radiografisch bestuurbaar speelgoed Futaba
- Radiografisch bestuurbaar speelgoed Graupner
- Radiografisch bestuurbaar speelgoed Little Tikes
- Radiografisch bestuurbaar speelgoed MJX
- Radiografisch bestuurbaar speelgoed Multiplex
- Radiografisch bestuurbaar speelgoed Parrot
- Radiografisch bestuurbaar speelgoed Proline
- Radiografisch bestuurbaar speelgoed Reely
- Radiografisch bestuurbaar speelgoed Revell
- Radiografisch bestuurbaar speelgoed Robbe
- Radiografisch bestuurbaar speelgoed SAB
- Radiografisch bestuurbaar speelgoed Sharper Image
- Radiografisch bestuurbaar speelgoed Spektrum
- Radiografisch bestuurbaar speelgoed TacTic
- Radiografisch bestuurbaar speelgoed Tamiya
- Radiografisch bestuurbaar speelgoed Velleman
- Radiografisch bestuurbaar speelgoed WLtoys
- Radiografisch bestuurbaar speelgoed JR
- Radiografisch bestuurbaar speelgoed Overmax
- Radiografisch bestuurbaar speelgoed Conrad
- Radiografisch bestuurbaar speelgoed Chicco
- Radiografisch bestuurbaar speelgoed Carrera
- Radiografisch bestuurbaar speelgoed Biltema
- Radiografisch bestuurbaar speelgoed Lenoxx
- Radiografisch bestuurbaar speelgoed Carson
- Radiografisch bestuurbaar speelgoed Ninco
- Radiografisch bestuurbaar speelgoed Traxxas
- Radiografisch bestuurbaar speelgoed ARRMA
- Radiografisch bestuurbaar speelgoed Spin Master
- Radiografisch bestuurbaar speelgoed ParkZone
- Radiografisch bestuurbaar speelgoed JETI
- Radiografisch bestuurbaar speelgoed SkyRC
- Radiografisch bestuurbaar speelgoed LRP
- Radiografisch bestuurbaar speelgoed Ripmax
- Radiografisch bestuurbaar speelgoed Maverick
- Radiografisch bestuurbaar speelgoed Axial
- Radiografisch bestuurbaar speelgoed Hangar 9
- Radiografisch bestuurbaar speelgoed FMS
- Radiografisch bestuurbaar speelgoed E-flite
- Radiografisch bestuurbaar speelgoed Flyzone
- Radiografisch bestuurbaar speelgoed Losi
- Radiografisch bestuurbaar speelgoed XciteRC
- Radiografisch bestuurbaar speelgoed FrSky
- Radiografisch bestuurbaar speelgoed Force Engine
- Radiografisch bestuurbaar speelgoed Vaterra
- Radiografisch bestuurbaar speelgoed Jada
- Radiografisch bestuurbaar speelgoed HPI Racing
- Radiografisch bestuurbaar speelgoed Kyosho
- Radiografisch bestuurbaar speelgoed PowerBox Systems
- Radiografisch bestuurbaar speelgoed Hobby Zone
- Radiografisch bestuurbaar speelgoed RC4WD
- Radiografisch bestuurbaar speelgoed Sky Rider
- Radiografisch bestuurbaar speelgoed DF-Models
- Radiografisch bestuurbaar speelgoed ROCHOBBY
Nieuwste handleidingen voor Radiografisch bestuurbaar speelgoed

31 Maart 2025

30 Maart 2025

30 Maart 2025

29 Maart 2025

29 Maart 2025

29 Maart 2025

29 Maart 2025

29 Maart 2025

29 Maart 2025

29 Maart 2025