Festo DGSC-6-10-P-P Handleiding
Festo
Boormachine
DGSC-6-10-P-P
Lees hieronder de 📖 handleiding in het Nederlandse voor Festo DGSC-6-10-P-P (3 pagina's) in de categorie Boormachine. Deze handleiding was nuttig voor 20 personen en werd door 2 gebruikers gemiddeld met 4.5 sterren beoordeeld
Pagina 1/3
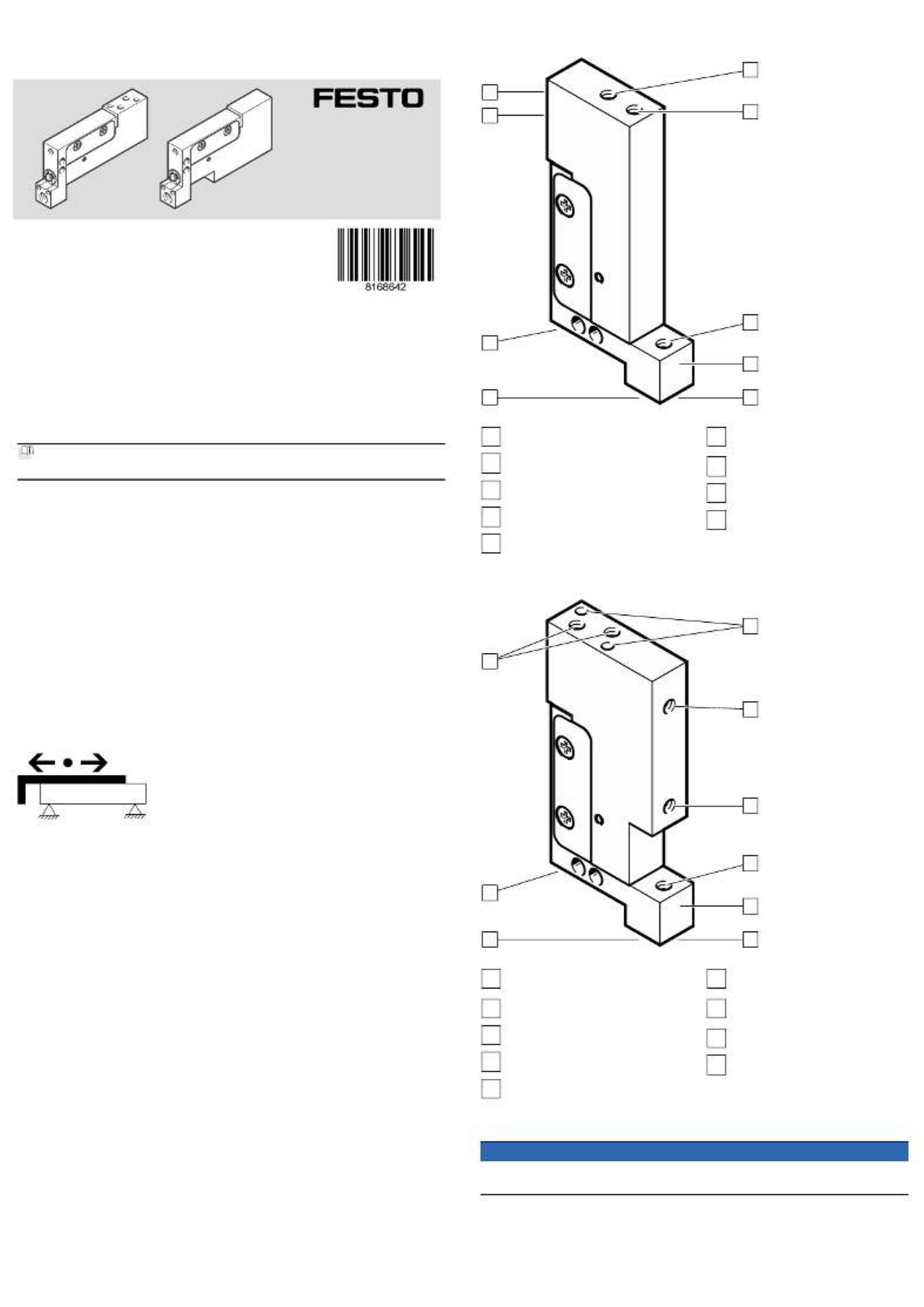
DGSC-6-10-P-...
Mini-slide
Festo SE & Co. KG
Ruiter Straße 82
73734 Esslingen
Deutschland
+49 711 347-0
www.festo.com
Operating instructions
8168642
2022-02b
[8168644]
Translation of the original instructions
© 2022 all rights reserved to Festo SE & Co. KG
1 Applicable Documents
All available documents for the product
è www.festo.com/sp.
2 Safety
2.1 Safety instructions
–Take into account the ambient conditions at the location of use.
–Only use the product in its original condition without unauthorised modifica-
tions.
–Observe the identifications on the product.
–Store the product in a cool, dry environment protected from UV and corrosion.
Keep storage times short.
–Before working on the product, switch off the compressed air supply and lock it
to prevent it from being switched on again.
–Have the product repaired by the Festo repair service only.
–Observe the tightening torques. Unless otherwise specified, the tolerance is
± 20%.
2.2 Intended use
The product is intended for the space-saving transport of masses. The product is
approved for slide operating mode.
Fig.1
2.3 Training of qualified personnel
Work on the product may only be carried out by qualified personnel who can
evaluate the work and detect dangers. The qualified personnel have skills and
experience in dealing with pneumatic (open-loop) control technology.
3 Additional information
–Contact the regional Festo contact if you have technical problems
è www.festo.com.
–Accessories and spare parts è www.festo.com/catalogue.
4 Product overview
4.1 Function
The product is a non-rotating single-piston drive with bearing guide.
The slide is moved back and forth by alternate pressurisation of the supply ports.
In the retracted end position, the slide is braked by elastic cushioning rings with
a mechanical fixed stop. In the extended end position, an integrated spring serves
as stroke compensation to avoid high forces on the workpiece during handling.
4.2 Product design
DGSC-6-10-PL
1
5
3
6
2
4
7
8
9
Fig. 2: Product design DGSC-6-10-PL
1
Supply port retracting
2
Supply port extending
3
Vacuum port
4
Slide
5
Centre hole 1.5 mm according to
DIN 6325, 2x
6
M5 thread for suction cup with
connection or mounting
7
M3 thread, e.g. for tubing holder
8
M3 thread for mounting, 2x
9
Centre hole 2 mm according to
DIN 6325, 2x
DGSC-6-10-PP
1
9
2
3
4
7
8
5
6
Fig. 3: Product design DGSC-6-10-P-P
1
Centre hole 2 mm according to
DIN 6325
2
Supply port extending
3
Supply port retracting
4
Vacuum port
5
Slide
6
Centre hole 1.5 mm according to
DIN 6325
7
M5 thread for suction cup with
connection or mounting
8
M3 thread, e.g. for tubing holder
9
M3 thread for mounting
5 Transport
NOTICE
Unexpected and unbraked movement of components
• Secure moving components for transport.
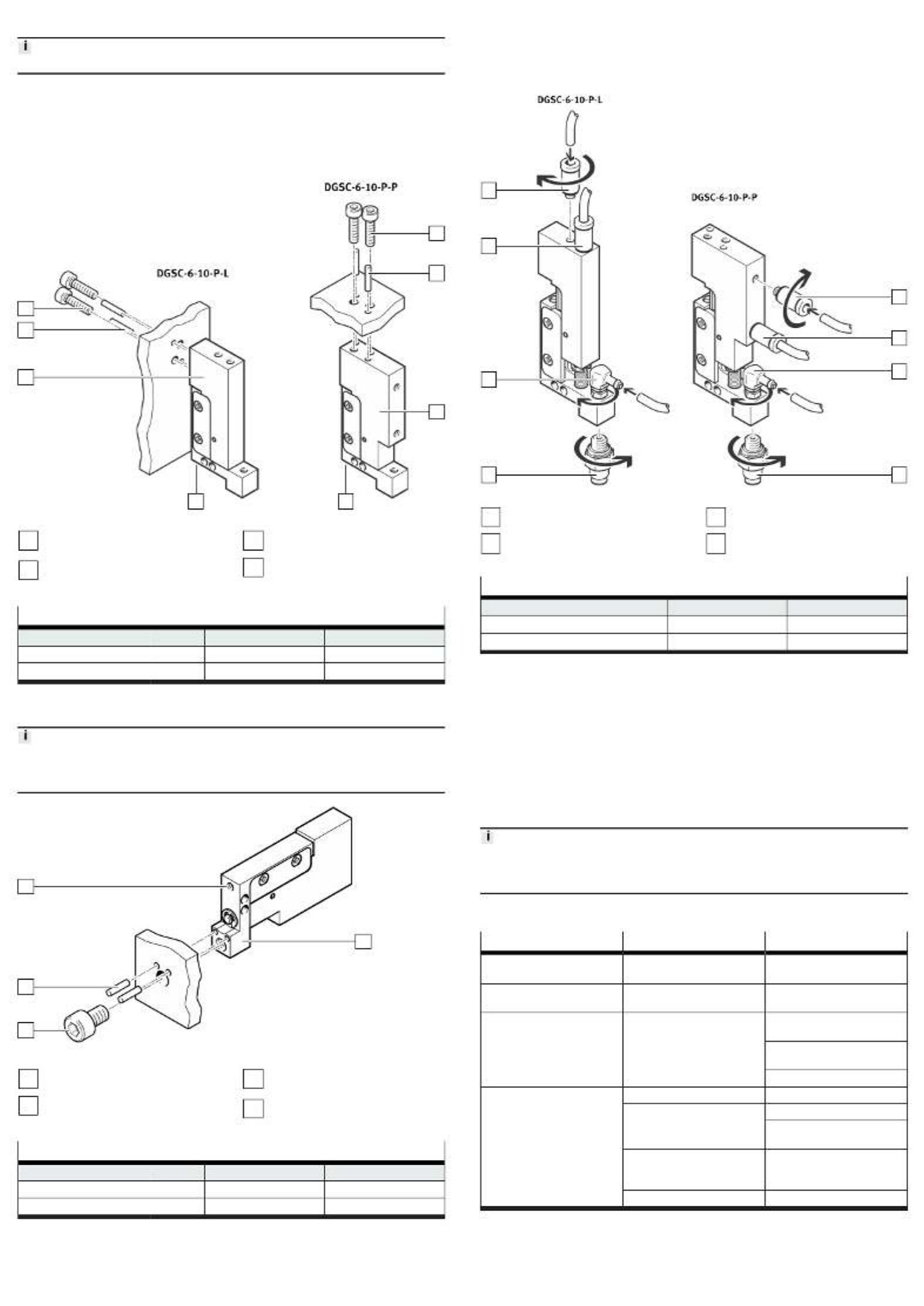
6 Mounting
The product can be attached to the housing or the slide.
• Use suitable fastening material depending on the type of mounting.
• Observe the maximum screw-in length of the screws.
• Mount the product according to the type of mounting.
• Maintain the maximum tightening torques.
• Mount the product without tension.
Mounting on the housing
1
1
2
2
3
3
4 4
Fig. 4: Mounting on the housing
1
M3 screw according to DIN 912,
2x
2
Cylindrical pin 2 mm according to
DIN 6325, 2x
3
Housing
4
M3 thread, e.g. for tubing holder
Screw-in length and tightening torque
Position 1 4
Max. screw-in length [mm] 4.5 4.0
Max. tightening torque [Nm] 1.2 1.2
Tab. 1: Screw-in length and tightening torque
Mounting on slide
• Support the slide from the opposite side when pressing in the cylindrical pins.
• When tightening the screw on the slide, counterhold with an 8 mm open-ended
spanner.
1
3
2
4
Fig. 5: Mounting on the slide, DGSC-6-10-PP as an example
1
Slide
2
M5 screw according to DIN 912,
2x
3
Cylindrical pin 1.5 mm according
to DIN 6325, 2x
4
M3 thread, e.g. for tubing holder
Screw-in length and tightening torque
Position 3 4
Max. screw-in length [mm] 4.0 4.0
Max. tightening torque [Nm] 5.9 1.2
Tab. 2: Screw-in length and tightening torque
7 Installation
1. Screw suitable fittings or accessories into the pneumatic ports. Maintain the
maximum tightening torques.
2. Connect tubing to the pneumatic ports.
1
2
2
1
3
3
44
Fig. 6: Installation
1
Supply port extending
2
Supply port retracting
3
Vacuum port
4
Suction cup with connection
Connection thread and tightening torques
Position , , 1 2 3 4
Connecting thread M3 M5
Max. tightening torque [Nm] 1.2 5.9
Tab. 3: Connection thread and tightening torques
8 Commissioning
• Pressurise the product slowly.
9 Maintenance
9.1 Cleaning
• Clean the product as required with a clean soft cloth and suitable cleaning
agents compatible to the material.
9.2 Lubrication
The product is initially lubricated.
Recommendation:
• Regrease the guide after 5 million cycles.
10 Fault clearance
Fault description Cause Remedy
The slide moves unevenly. The one-way flow control valves
are not installed correctly.
Control the exhaust air flow.
The slide is in initial position
despite pressurisation.
The tubing is faulty. Check the tubing.
The slide speed is too low. The air volume is insufficient. Increase the connection cross-
sections.
Check the flow control valve
setting.
Connect a volume upstream.
The slide stops in the end posi-
tion without cushioning.
The speed is too high. Reduce the speed.
The cushioning is too low. Reduce the speed.
Check the cushioning rings and
replace if necessary.
The air cushion is not present. Pressurise both supply ports
simultaneously, then exhaust
one side.
The payload is too high. Reduce the payload.
Tab. 4: Fault clearance
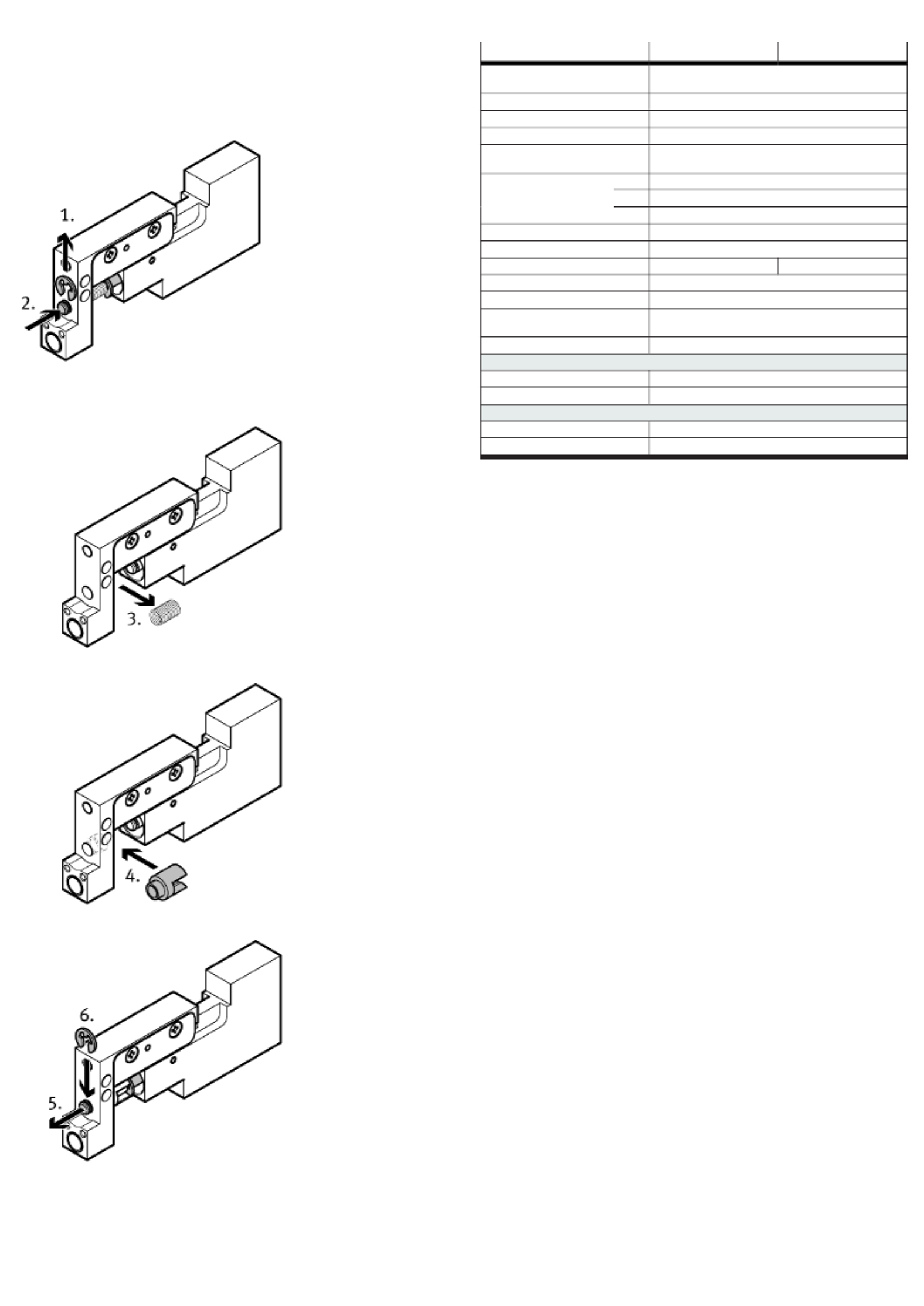
11 Modification
In its delivery status the product is equipped with a spring for stroke compen-
sation. Replacing the spring with the enclosed blue spacer allows the stroke
compensation of the extended end position to be suppressed and converted to a
fixed stop.
• Shut off the compressed air supply and lock to prevent reactivation.
Conversion to fixed stop
Fig.7
1. Remove the shaft circlip.
2. Push in the shaft.
3. Remove the spring.
4. Insert the enclosed blue spacer in the correct position.
5. Slide out the shaft.
6. Install the shaft circlip.
12 Technical data
DGSC-6-10-P-... -L -P
Design Double-acting drive with Scotch yoke system and ball
bearing cage guide
Mounting position Any
Cushioning Elastic cushioning ring on both sides
Operating medium Compressed air to ISO 8573-1:2010 [7:4:4]
Information on the operating
medium
lubricated operation possible, in which case lubricated
operation will always be required
Operating pressure [MPa] 0.1 … 0.6
[bar] 1.0 … 6.0
[psi] 14.5 … 87.0
Ambient temperature [°C] 10 … 50
Repetition accuracy [mm] 0.2<
Product weight [g] 42 52
Moving mass [g] 17
Max. payload [g] 30
Length of stroke compensa-
tion via spring
[mm] –2.5 ± 1
Max. forces and torques è www.festo.com/catalogue
Theoretical force at 0.6 MPa (6 bar, 87 psi)
Extending [N] 17.0
Retracting [N] 12.7
Materials
Piston rod, housing High-alloy stainless steel
Seals Nitrile rubber
Tab. 5: Technical data
Product specificaties
Merk: | Festo |
Categorie: | Boormachine |
Model: | DGSC-6-10-P-P |
Heb je hulp nodig?
Als je hulp nodig hebt met Festo DGSC-6-10-P-P stel dan hieronder een vraag en andere gebruikers zullen je antwoorden
Handleiding Boormachine Festo

21 November 2024
Handleiding Boormachine
- Boormachine Bosch
- Boormachine IKEA
- Boormachine Panasonic
- Boormachine AEG
- Boormachine DeWalt
- Boormachine Baier
- Boormachine Basetech
- Boormachine Batavia
- Boormachine Bavaria
- Boormachine Berner
- Boormachine Black Decker
- Boormachine Blucave
- Boormachine Bort
- Boormachine Bruder Mannesmann
- Boormachine Defort
- Boormachine Delta
- Boormachine Dremel
- Boormachine Duro
- Boormachine Duro Pro
- Boormachine Ecomac
- Boormachine Economy
- Boormachine Einhell
- Boormachine Elu
- Boormachine Fe Powertools
- Boormachine Fein
- Boormachine Felisatti
- Boormachine Ferm
- Boormachine Ferrex
- Boormachine Festool
- Boormachine Flex
- Boormachine Gamma
- Boormachine Global
- Boormachine Goon
- Boormachine Gude
- Boormachine Hikoki
- Boormachine Hitachi
- Boormachine Holzmann
- Boormachine Huvema
- Boormachine Hyundai
- Boormachine Kawasaki
- Boormachine Kinzo
- Boormachine Kraftronic
- Boormachine Kress
- Boormachine Laserliner
- Boormachine Lux Tools
- Boormachine Luxor
- Boormachine Maestro
- Boormachine Makita
- Boormachine Maktec
- Boormachine Max
- Boormachine Metabo
- Boormachine Milwaukee
- Boormachine Parkside
- Boormachine Powerfix
- Boormachine Powerplus
- Boormachine Profitech
- Boormachine Protool
- Boormachine Robust
- Boormachine Rupes
- Boormachine Ryobi
- Boormachine Scheppach
- Boormachine Silverline
- Boormachine Skil
- Boormachine Sparky
- Boormachine Spit
- Boormachine Stanley
- Boormachine Stihl
- Boormachine Stomer
- Boormachine Tanaka
- Boormachine Texas
- Boormachine Toolcraft
- Boormachine Toolland
- Boormachine Topcraft
- Boormachine Trotec
- Boormachine Varo
- Boormachine Velleman
- Boormachine Vonroc
- Boormachine Westfalia
- Boormachine Workzone
- Boormachine Worx
- Boormachine Wurth
- Boormachine Zipper
- Boormachine Ozito
- Boormachine Clas Ohlson
- Boormachine Black And Decker
- Boormachine Steren
- Boormachine Cocraft
- Boormachine Meec Tools
- Boormachine Genesis
- Boormachine Carat
- Boormachine Eibenstock
- Boormachine Hilti
- Boormachine Cotech
- Boormachine Power Craft
- Boormachine Tacklife
- Boormachine Truper
- Boormachine Fieldmann
- Boormachine Mafell
- Boormachine Proxxon
- Boormachine Biltema
- Boormachine Malmbergs
- Boormachine Porter-Cable
- Boormachine Sun Joe
- Boormachine Dedra
- Boormachine Graphite
- Boormachine Narex
- Boormachine RIDGID
- Boormachine Tryton
- Boormachine Herkules
- Boormachine MSW
- Boormachine Sthor
- Boormachine Craftsman
- Boormachine Rikon
- Boormachine Cecotec
- Boormachine Verto
- Boormachine Alpha Tools
- Boormachine Hazet
- Boormachine G-Technology
- Boormachine Yato
- Boormachine Total
- Boormachine Stalco
- Boormachine Baumr-AG
- Boormachine Powerblade
- Boormachine Meister Craft
- Boormachine King Craft
- Boormachine Max Bahr
- Boormachine Toolson
- Boormachine Wolfcraft
- Boormachine Kreg
- Boormachine Rok
- Boormachine Netter Vibration
- Boormachine RUKO
- Boormachine Einhell Bavaria
- Boormachine McKenzie
- Boormachine Proviel
- Boormachine Ribimex
- Boormachine Ergotools Pattfield
- Boormachine MyTool
- Boormachine Rodcraft
- Boormachine Bavaria By Einhell
- Boormachine Handwerk
Nieuwste handleidingen voor Boormachine

31 Maart 2025

28 Maart 2025

28 Maart 2025

28 Maart 2025

28 Maart 2025

28 Maart 2025

28 Maart 2025

28 Maart 2025

28 Maart 2025

28 Maart 2025