Festo DFPD-10 Handleiding
Festo
Meetapparatuur
DFPD-10
Lees hieronder de 📖 handleiding in het Nederlandse voor Festo DFPD-10 (5 pagina's) in de categorie Meetapparatuur. Deze handleiding was nuttig voor 51 personen en werd door 2 gebruikers gemiddeld met 4.5 sterren beoordeeld
Pagina 1/5
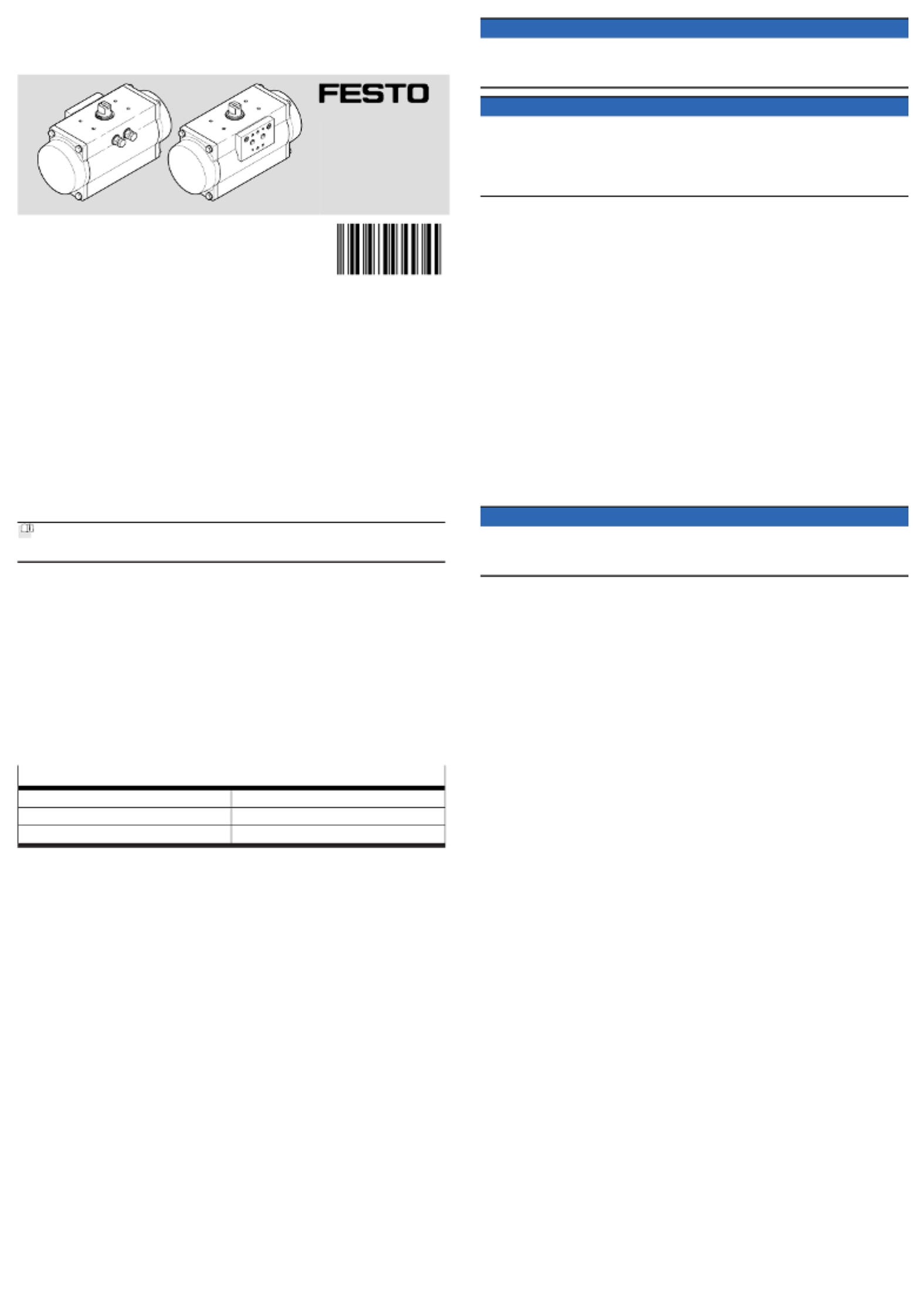
DFPD-...
Semi-rotary drive
Festo SE & Co. KG
Ruiter Straße 82
73734 Esslingen
Germany
+49 711 347-0
www.festo.com
Operating instruction
8202412
2023-11f
[8202414]
8202412
Translation of the original instructions
© 2023 all rights reserved to Festo SE & Co. KG
1 About this document
1.1 Purpose of the document
This document describes the use of the above-mentioned product. It contains
additional information for the use of the product in safety-related systems (safety
manual in accordance with IEC61508).
1.2 Applicable documents
All available documents for the product
èwww.festo.com/sp.
1.3 Target group
This document is targeted towards individuals who mount and operate the
product. It is additionally targeted towards individuals who are entrusted with
the planning and application of the product in a safety-oriented system.
1.4 Product version
This document refers to the standard version of the quarter turn actuator DFPD of
the following product versions.
–DFPD-10…-2300: product labelling without revision number
–DFPD-10…-300: product labelling with revision number [Rev.01]
This document does not apply to the variants DFPD-…-T4 and DFPD-…-T6 with
extended temperature range.
1.5 Specified standards
Version
IEC 61508-1:2010 IEC 61508-7:2010
IEC 61508-2:2010 IEC 61511:2016
IEC 61508-4:2010
Tab. 1: Specified standards
2 Safety
2.1 General safety instructions
–Only use the product in its original condition without unauthorised modifica-
tions.
–Only use the product if it is in perfect technical condition.
–Observe the identifications on the product.
–Before working on the product, switch off the compressed air supply and lock it
to prevent it from being switched on again.
–Take into account the ambient conditions at the location of use. Corrosive
environments reduce the service life of the product.
–Protect the product from fluctuations in pressure: use a pressure control valve.
Return to Festo
Hazardous substances can endanger the health and safety of persons and cause
damage to the environment. To prevent hazards, the product should only be
returned if explicitly requested by Festo.
–Consult your regional Festo contact.
–Complete the declaration of contamination and attach it to the outside of the
packaging.
–Comply with all legal requirements for the handling of hazardous substances
and the transport of dangerous goods.
2.2 Intended use
The quarter-turn actuator operates process valves in fluid systems, (e.g. ball
valves or butterfly valves).
NOTICE
The operating torque of the actuator must not be greater than the maximum
permissible torque specified in ISO5211 in relation to the size of the mounting
flange and coupling.
NOTICE
Depending on the design, part-turn actuators that are moved to a defined
switching position by spring force in a de-energised state lose at least 30% of
their calculated torque as a result of the relaxation of the spring assemblies and
friction.
• Take an appropriate safety factor into account in the application.
2.3 Training of qualified personnel
Work on the product may only be carried out by qualified personnel who can
evaluate the work and detect dangers. The qualified personnel have knowledge
and experience in process automation.
3 Additional information
–Contact the regional Festo contact if you have technical problems
èwww.festo.com.
–Accessories and spare parts èwww.festo.com/catalogue.
4 Information on functional safety
4.1 Achievable safety classification
The product is suitable for use as an element in a safety-related system in accord-
ance with IEC61511.
–In Low Demand Mode up to SIL2
–In High Demand Mode up to SIL1
Taking into account the required minimum hardware fault tolerance (HFT=1), the
product can also be used up to SIL3 in a redundant configuration of the entire
system.
NOTICE
The suitability for certain applications can only be determined in connection with
the assessment of further components of the subsystem. These must achieve the
same safety level.
4.2 Safety function
Double-acting semi-rotary drives DFPD-...-RD/-LD
The safety function is to switch the actuator to the defined safety switching
position. This switching movement is achieved by pressurising the corresponding
pressure chamber with compressed air. The value of the torque generated
depends on the pressure difference between the two pressure chambers sepa-
rated by the piston.
Single-acting semi-rotary drives DFPD-...-RS/-LS
The safety function is to switch the actuator to the defined safety switching
position when the compressed air is switched off and the spring chamber is
exhausted. This switching movement is achieved through the spring force of the
spring assembly.
4.3 Operating conditions
–General information on safe operation
è2Safety.
–Periodic tests (function test) è11Maintenance, è11.1 General.
–Ambient conditions and other technical specifications è15Technical data.
4.4 Limitations of use
If used in a safety-related system, the service life is limited to 8years subject to
compliance with the operating conditions.
–Recommended interval for a complete function test: 1year
–Maximum permissible interval for a complete function test: 3years
When a function test is negative, maintenance work must be carried out immedi-
ately.
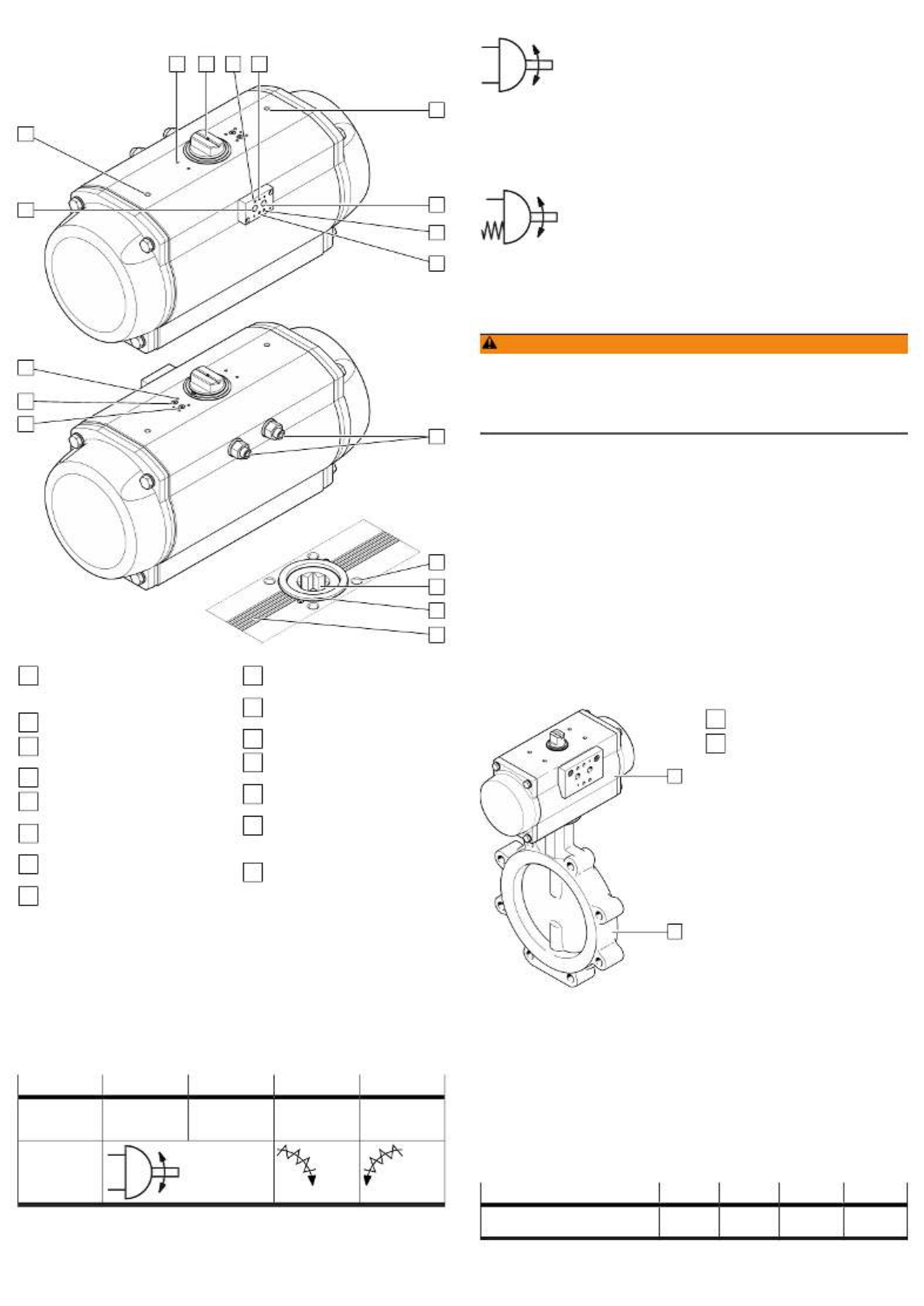
5 Product overview
5.1 Product structure
4
6
3
4
15
32
5
14
7
8
9
10
11
12
13
5
1
Fig. 1: Product structure (taking DFPD-2300 as an example)
1
Mounting thread for limit switch
or position sensor in accordance
with VDI/VDE 3845-1
2
Transmission shaft
3
Mounting thread for NAMUR
interface
4
Mounting thread for coding pin
5
Thread for transport lugs
(DFPD-2300 only)
6
Supply port 4 when the NAMUR
interface is used
7
End-position adjustment on both
sides
8
Mounting thread for process
valve in accordance with
ISO 5211
9
Coupling for process valve in
accordance with ISO 5211
10
Centering ring for mounting on
adapter bridge, DFPD-...-C only
11
Leakage slot
12
Supply port 2 when the VDE2
interface is used
13
Supply port 4, when the VDE2
interface is used
14
Mounting thread for
adapter in accordance with
VDI 3847-2 , DFPD-...-VDE2 only
15
Supply port 2 when the NAMUR
interface is used
A shaft projects outward through the housing on both sides. It transmits the
reaction torque to a process valve and, if applicable, a limit switch or position
sensor. The end stops can be adjusted in the range of 5° thanks to end-position
adjustment on both sides.
5.2 Function
The piston movement of the quarter-turn actuator is converted into a swivel move-
ment of the transmission shaft by Rack & Pinion kinematics (gear rack/pinion).
The swivel angle is 90° to a maximum of 180°, depending on the product version.
DFPD-... -RD -LD -RS -LS
Mode of operation Double-acting,
closes to the right
Double-acting,
closes to the left
Single-acting
(spring return),
closes to the right
Single-acting
(spring return),
closes to the left
Symbol on product
label
Tab. 2: Product version and mode of operation
Double-acting quarter-turn actuator: DFPD-...-RD/-LD
Fig. 2: Symbol for double-acting quarter-turn actuator
The switching movement is achieved by pressurising the corresponding pressure
chamber with compressed air. The value of the torque generated depends on the
pressure difference between the two pressure chambers separated by the piston.
Single-acting quarter-turn actuator: DFPD-...-RS/-LS
Fig. 3: Symbol for single-acting quarter-turn actuator
The switching movement is achieved through the spring force of the spring
assembly.
6 Transport
WARNING
Danger of crushing. Danger of shearing.
Body parts can be crushed or severed if the product falls.
• Use appropriate load handling equipment.
• For DFPD-2300: screw suitable transport lugs into the specified threaded holes.
Lift the drive by the transport lugs.
When dispatching used products, comply with all legal requirements for the han-
dling of hazardous substances and the transport of dangerous goods
è2Safety.
7 Storage
–Remove all attachments.
–Store the product in a cool, dry environment protected from UV and corrosion.
Keep storage times short.
–Note the ambient and storage conditions.
–When storing for a long period, test that the product is working at regular
intervals.
–Seal the pneumatic ports.
–Protect the coupling parts with grease or protective oil.
–Store the product on a level wooden pallet to prevent damage to the coupling
flange.
8 Assembly
8.1 Assembly without adapter bridge
1
2
Fig. 4: Assembly without adapter
bridge
1
Quarter-turn actuator
2
Process valve
1. Prepare the process valve.
Adjust the control shaft of the process valve to implement the desired oper-
ating method for opening and closing.
2. Place the quarter-turn actuator on the control shaft of the process valve.
ÄThe control shaft must sit in the coupling of the quarter-turn actuator
without tilting è5.1 Product structure.
3. Mount the quarter-turn actuator on the connecting flange of the process valve
using 4 corrosion-resistant screws and retaining rings.
4. Tighten the screws crosswise to the tightening torque. Note the flange type of
the quarter-turn actuator.
DFPD-... -F03 -F04 -F05 -F07
Tightening torque for the
screws
[Nm] 5.5±0.5 5.5±0.5 9.5±0.5 23±1
Tab. 3: Tightening torques for the flange, DFPD-...-F03…-F07
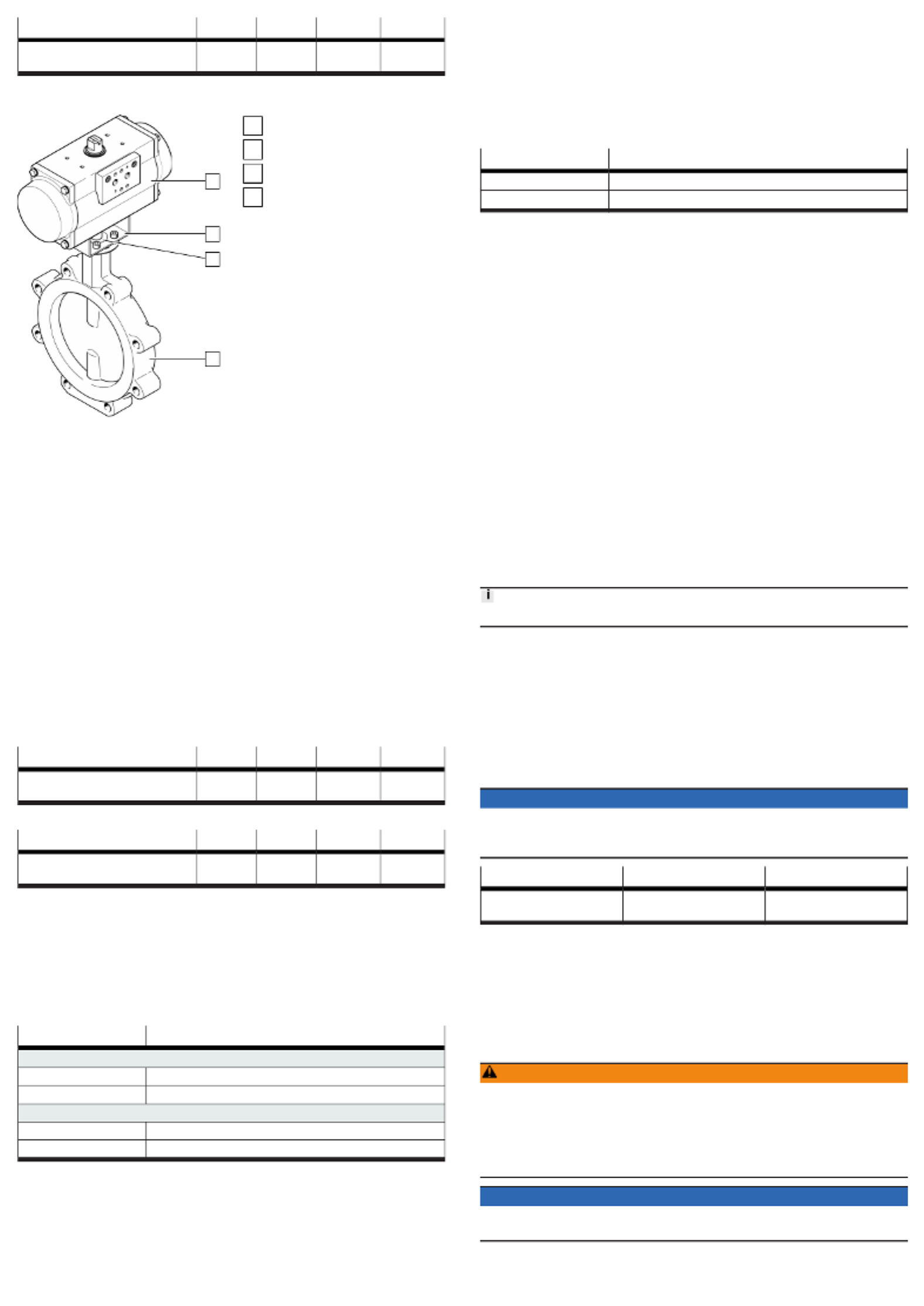
DFPD-... -F10 -F12 -F14 -F16
Tightening torque for the
screws
[Nm] 48±2 82±2 195±5 380±10
Tab. 4: Tightening torques for the flange, DFPD-...-F10…-F16
8.2 Assembly with adapter bridge
1
2
3
4
Fig. 5: Assembly with adapter bridge
1
Quarter-turn actuator
2
Adapter bridge
3
Coupling
4
Process valve
1. Have the adapter bridge and coupling ready
èwww.festo.com/catalogue.
2. Mount the adapter bridge on the quarter-turn actuator.
–Align the studs of the adapter bridge lengthwise to the quarter-turn
actuator.
–Align the open side of the adapter bridge with the process valve.
–Do not jam the centering ring in the drilled hole for the adapter bridge.
–Screw in the screws, but do not tighten them yet.
3. Prepare the process valve.
Adjust the control shaft of the process valve to implement the desired oper-
ating method for opening and closing.
4. Insert the coupling.
ÄThe square of the coupling must sit in the coupling of the quarter-turn
actuator without tilting è5.1 Product structure.
5. Place the quarter-turn actuator with the adapter bridge and coupling on the
control shaft of the process valve.
ÄThe square of the process valve must sit in the coupling without tilting.
6. Mount the adapter bridge on the connecting flange of the process valve using
4 corrosion-resistant screws, retaining rings and nuts.
7. Tighten the screws on the quarter-turn actuator and the process valve cross-
wise to the tightening torque. Note the flange type of the part-turn actuator.
DFPD-... -F03 -F04 -F05 -F07
Tightening torque for the
screws
[Nm] 5.5±0.5 5.5±0.5 9.5±0.5 23±1
Tab. 5: Tightening torques for the flange, DFPD-...-F03…-F07
DFPD-... -F10 -F12 -F14 -F16
Tightening torque for the
screws
[Nm] 48±2 82±2 195±5 380±10
Tab. 6: Tightening torques for the flange, DFPD-...-F10…-F16
9 Installation
9.1 Double-acting quarter-turn actuator: DFPD-...-RD/-LD
Depending on the form of attachment chosen, supply ports are available on the
housing or on the NAMUR interface è5.1 Product structure.
1. Connect the air supply to supply port 2 and supply port4.
2. Seal unused supply ports with blind plugs.
Supply port Effect1)
DFPD-...-RD
2 Air supply, anti-clockwise direction of rotation
4 Air supply, clockwise direction of rotation
DFPD-...-LD
2 Air supply, clockwise direction of rotation
4 Air supply, anti-clockwise direction of rotation
1) Direction of rotation from the connection point of the accessory.
Tab. 7: Supply port for the double-acting quarter-turn actuator
9.2 Single-acting quarter-turn actuator: DFPD-...-RS/-LS
Depending on the form of attachment chosen, supply ports are available on the
housing or on the NAMUR interface è5.1 Product structure.
1. Prevent a corrosive atmosphere in the spring chamber. Use a rebreather block
if the atmosphere is corrosive.
2. To prevent dirt from penetrating, fasten a filter element to supply port4.
3. Connect the air supply to supply port2.
4. Seal unused supply ports with blind plugs.
Supply port Effect
2 Air supply; always connected
4 Pressurisation of spring chamber
Tab. 8: Supply port for single-acting quarter-turn actuator
10 Commissioning
Requirement: The quarter-turn actuator must be fully assembled and connected.
1. Ventilate the quarter-turn actuator slowly.
2. Check that it is working correctly at a low speed:
–Direction of rotation of the quarter-turn actuator
–Position of the process valve
11 Maintenance
11.1 General
Low Demand Mode:
–The product is maintenance-free in intended use.
High Demand Mode:
–Check that the product is working properly at regular intervals. The check
interval depends on the operating conditions.
11.2 Proof test (Proof Test)
The proof test consists of a Full Stroke test of the actuator. Full rotation of
the shaft is tested at the connection to the process valve dependent on the
switching position of the control valve. The switching position of the shaft can
be determined visually (position of the shaft groove) using a position sensor or
something else suitable.
–Carry out the proof test at least once every 3 years.
During the proof test, the safety of the application must be ensured.
1. Trigger the rotation of the shaft at the control valve.
2. Measure the time taken until the quarter-turn actuator has caused the shaft
to rotate fully.
ÄThe test is successful if the quarter-turn actuator completes the move-
ment within the switching time intended for control by the control valve.
3. Check the actuator externally (visual inspection).
ÄThe test is successful if no defect, leakage or contamination is detected.
4. Document the test results.
12 Malfunctions
NOTICE
Repairs to the product are not permissible. In the event of malfunctions or failure:
Replace the product and let Festo know about the failure. Return defective prod-
ucts to Festo.
Malfunction Cause Remedy
The actuator will not move in the
desired direction.
The supply ports are not con-
nected correctly.
–Adjust the tubing.
Tab. 9: Fault clearance
13 Modification
13.1 Replacing the spring assembly for DFPD-...-RS/-LS
Requirements
–The mounting position is vertical. The quarter turn actuator is secured against
tipping.
–The quarter turn actuator is demounted è14 Disassembly.
WARNING
Risk of injury from flying objects.
A faulty spring package can result in the cover being ejected during disassembly
and causing injury.
• If the cover is still under spring force when the gap width is reached, do not
proceed with the disassembly.
• Replace the actuator.
NOTICE
Plastic deformation of the screws
• Replace the screws after loosening them
èwww.festo.com/spareparts.
Product specificaties
Merk: | Festo |
Categorie: | Meetapparatuur |
Model: | DFPD-10 |
Heb je hulp nodig?
Als je hulp nodig hebt met Festo DFPD-10 stel dan hieronder een vraag en andere gebruikers zullen je antwoorden
Handleiding Meetapparatuur Festo

21 November 2024

21 November 2024
Handleiding Meetapparatuur
- Meetapparatuur Bosch
- Meetapparatuur IKEA
- Meetapparatuur Panasonic
- Meetapparatuur DeWalt
- Meetapparatuur Fysic
- Meetapparatuur Honeywell
- Meetapparatuur Pioneer
- Meetapparatuur Topcom
- Meetapparatuur ABB
- Meetapparatuur Ade
- Meetapparatuur Aktobis
- Meetapparatuur Albrecht
- Meetapparatuur Alecto
- Meetapparatuur Amprobe
- Meetapparatuur Ansmann
- Meetapparatuur AS - Schwabe
- Meetapparatuur Basetech
- Meetapparatuur Be Cool
- Meetapparatuur Beha-Amprobe
- Meetapparatuur Benning
- Meetapparatuur Beurer
- Meetapparatuur Bresser
- Meetapparatuur Bruder Mannesmann
- Meetapparatuur Burg-Wachter
- Meetapparatuur Danfoss
- Meetapparatuur Digitus
- Meetapparatuur Duro Pro
- Meetapparatuur EBERLE
- Meetapparatuur Einhell
- Meetapparatuur Eizo
- Meetapparatuur Elgato
- Meetapparatuur Enda
- Meetapparatuur Entes
- Meetapparatuur Extech
- Meetapparatuur Finder
- Meetapparatuur Flex
- Meetapparatuur Flir
- Meetapparatuur Fluke
- Meetapparatuur Goclever
- Meetapparatuur Goobay
- Meetapparatuur Gossen Metrawatt
- Meetapparatuur Grohe
- Meetapparatuur Gude
- Meetapparatuur Hager
- Meetapparatuur Hama
- Meetapparatuur Holzmann
- Meetapparatuur Homedics
- Meetapparatuur Ideal
- Meetapparatuur IHealth
- Meetapparatuur Kern
- Meetapparatuur Kogan
- Meetapparatuur Kopp
- Meetapparatuur LaCie
- Meetapparatuur Laica
- Meetapparatuur Lanaform
- Meetapparatuur Laserliner
- Meetapparatuur Livington
- Meetapparatuur Logilink
- Meetapparatuur Maximum
- Meetapparatuur Megasat
- Meetapparatuur Megger
- Meetapparatuur Metrel
- Meetapparatuur Metrix
- Meetapparatuur Microlife
- Meetapparatuur Midland
- Meetapparatuur Milwaukee
- Meetapparatuur Mitsubishi
- Meetapparatuur Monacor
- Meetapparatuur Muller
- Meetapparatuur Nedis
- Meetapparatuur PCE
- Meetapparatuur PCE Instruments
- Meetapparatuur Perel
- Meetapparatuur Powerfix
- Meetapparatuur Pyle
- Meetapparatuur Reely
- Meetapparatuur RK Technology
- Meetapparatuur Rossmax
- Meetapparatuur Sanwa
- Meetapparatuur Schneider
- Meetapparatuur Sekonic
- Meetapparatuur Shimano
- Meetapparatuur Silvercrest
- Meetapparatuur Silverline
- Meetapparatuur Soehnle
- Meetapparatuur Steinberg
- Meetapparatuur Technics
- Meetapparatuur Techno Line
- Meetapparatuur Technoline
- Meetapparatuur TFA
- Meetapparatuur Toolland
- Meetapparatuur Trotec
- Meetapparatuur Truelife
- Meetapparatuur Uni-T
- Meetapparatuur VDO
- Meetapparatuur Velleman
- Meetapparatuur VirtuFit
- Meetapparatuur Voltcraft
- Meetapparatuur Wachendorff
- Meetapparatuur Westfalia
- Meetapparatuur Joy-it
- Meetapparatuur Omnitronic
- Meetapparatuur Oregon Scientific
- Meetapparatuur Black And Decker
- Meetapparatuur Continental Edison
- Meetapparatuur CSL
- Meetapparatuur Klein Tools
- Meetapparatuur Peak
- Meetapparatuur Cocraft
- Meetapparatuur Meec Tools
- Meetapparatuur Soler And Palau
- Meetapparatuur Sauter
- Meetapparatuur Proficare
- Meetapparatuur Eurolite
- Meetapparatuur SIIG
- Meetapparatuur RIDGID
- Meetapparatuur REV
- Meetapparatuur MSW
- Meetapparatuur SHX
- Meetapparatuur Victron Energy
- Meetapparatuur Carrier
- Meetapparatuur Fantini Cosmi
- Meetapparatuur Vemer
- Meetapparatuur Lund
- Meetapparatuur Testo
- Meetapparatuur Circutor
- Meetapparatuur Eastron
- Meetapparatuur Stabila
- Meetapparatuur Testboy
- Meetapparatuur Hazet
- Meetapparatuur Yato
- Meetapparatuur IFM
- Meetapparatuur Wago
- Meetapparatuur GW Instek
- Meetapparatuur Kyoritsu
- Meetapparatuur Dahua Technology
- Meetapparatuur Owon
- Meetapparatuur Eltako
- Meetapparatuur Cablexpert
- Meetapparatuur Wentronic
- Meetapparatuur Comark
- Meetapparatuur Clean Air Optima
- Meetapparatuur ORNO
- Meetapparatuur Multimetrix
- Meetapparatuur Etymotic
- Meetapparatuur Hameg
- Meetapparatuur PICO
- Meetapparatuur Sonel
- Meetapparatuur YSI
- Meetapparatuur TFA Dostmann
- Meetapparatuur Werma
- Meetapparatuur Greisinger
- Meetapparatuur Testec
- Meetapparatuur Hikmicro
- Meetapparatuur Vimar
- Meetapparatuur Kreg
- Meetapparatuur Kemo
- Meetapparatuur Pancontrol
- Meetapparatuur SRS
- Meetapparatuur H-Tronic
- Meetapparatuur Ebro
- Meetapparatuur X-Rite
- Meetapparatuur Tempest
- Meetapparatuur Arya
- Meetapparatuur PeakTech
- Meetapparatuur Tru Components
- Meetapparatuur Emko
- Meetapparatuur KS Tools
- Meetapparatuur Phoenix Contact
- Meetapparatuur Trumeter
- Meetapparatuur Aeros
- Meetapparatuur Delta Ohm
- Meetapparatuur Aqua Master Tools
- Meetapparatuur Hanna
- Meetapparatuur Atmel
- Meetapparatuur Qualita
- Meetapparatuur MGL Avionics
- Meetapparatuur Adwa
- Meetapparatuur Rigol
- Meetapparatuur Chauvin Arnoux
- Meetapparatuur Aim TTi
- Meetapparatuur AREXX
- Meetapparatuur UHoo
- Meetapparatuur CEM
- Meetapparatuur NEO Tools
- Meetapparatuur Jonard Tools
- Meetapparatuur TDE Instruments
- Meetapparatuur CESYS
- Meetapparatuur Angler
- Meetapparatuur Aerospace Logic
- Meetapparatuur Grundfos
- Meetapparatuur Zircon
- Meetapparatuur BJZ
- Meetapparatuur Johnson Level
- Meetapparatuur GMW
- Meetapparatuur SOEKS
- Meetapparatuur Rotronic
- Meetapparatuur Apollo Ultrasonic
- Meetapparatuur Softing
- Meetapparatuur Weltron
- Meetapparatuur Oscium
- Meetapparatuur Janitza
- Meetapparatuur Condtrol
- Meetapparatuur J.P. Instruments
- Meetapparatuur Weidmüller
- Meetapparatuur Ermenrich
- Meetapparatuur Siglent
- Meetapparatuur INFICON
- Meetapparatuur Qubino
- Meetapparatuur Lascar Electronics
- Meetapparatuur HT Instruments
- Meetapparatuur BAXTER
- Meetapparatuur P3 International
- Meetapparatuur Beckmann & Egle
- Meetapparatuur Seek Thermal
- Meetapparatuur Motrona
- Meetapparatuur Kübler
- Meetapparatuur AkYtec
- Meetapparatuur Tempo
- Meetapparatuur Camille Bauer
- Meetapparatuur Blebox
- Meetapparatuur Seaward
- Meetapparatuur HOZO Design
- Meetapparatuur Corentium
- Meetapparatuur GQ
- Meetapparatuur Tektronix
- Meetapparatuur Dostmann Electronic
- Meetapparatuur Murideo
- Meetapparatuur SecuTech
- Meetapparatuur NetPeppers
- Meetapparatuur SensoProtect
- Meetapparatuur Water-i.d.
- Meetapparatuur ZKETECH
- Meetapparatuur LabNation
- Meetapparatuur Electronics International
- Meetapparatuur Cliff
- Meetapparatuur ClimeMET
- Meetapparatuur Fixpoint
- Meetapparatuur Stahlwille
- Meetapparatuur MASIMO
- Meetapparatuur Milesight
- Meetapparatuur Noyafa
- Meetapparatuur Topex
- Meetapparatuur Stamos
- Meetapparatuur Brookhuis
- Meetapparatuur Senseca
- Meetapparatuur Crowcon
- Meetapparatuur Aeroqual
- Meetapparatuur Intact
- Meetapparatuur PQ Plus
- Meetapparatuur DriveTest
- Meetapparatuur Helvi
- Meetapparatuur Mitutoyo
Nieuwste handleidingen voor Meetapparatuur

3 April 2025

3 April 2025

3 April 2025

3 April 2025

3 April 2025

3 April 2025

3 April 2025

3 April 2025

3 April 2025

3 April 2025