Milwaukee 6742-20 Handleiding
Milwaukee
Schroefmachine
6742-20
Lees hieronder de 📖 handleiding in het Nederlandse voor Milwaukee 6742-20 (13 pagina's) in de categorie Schroefmachine. Deze handleiding was nuttig voor 45 personen en werd door 2 gebruikers gemiddeld met 4.5 sterren beoordeeld
Pagina 1/13
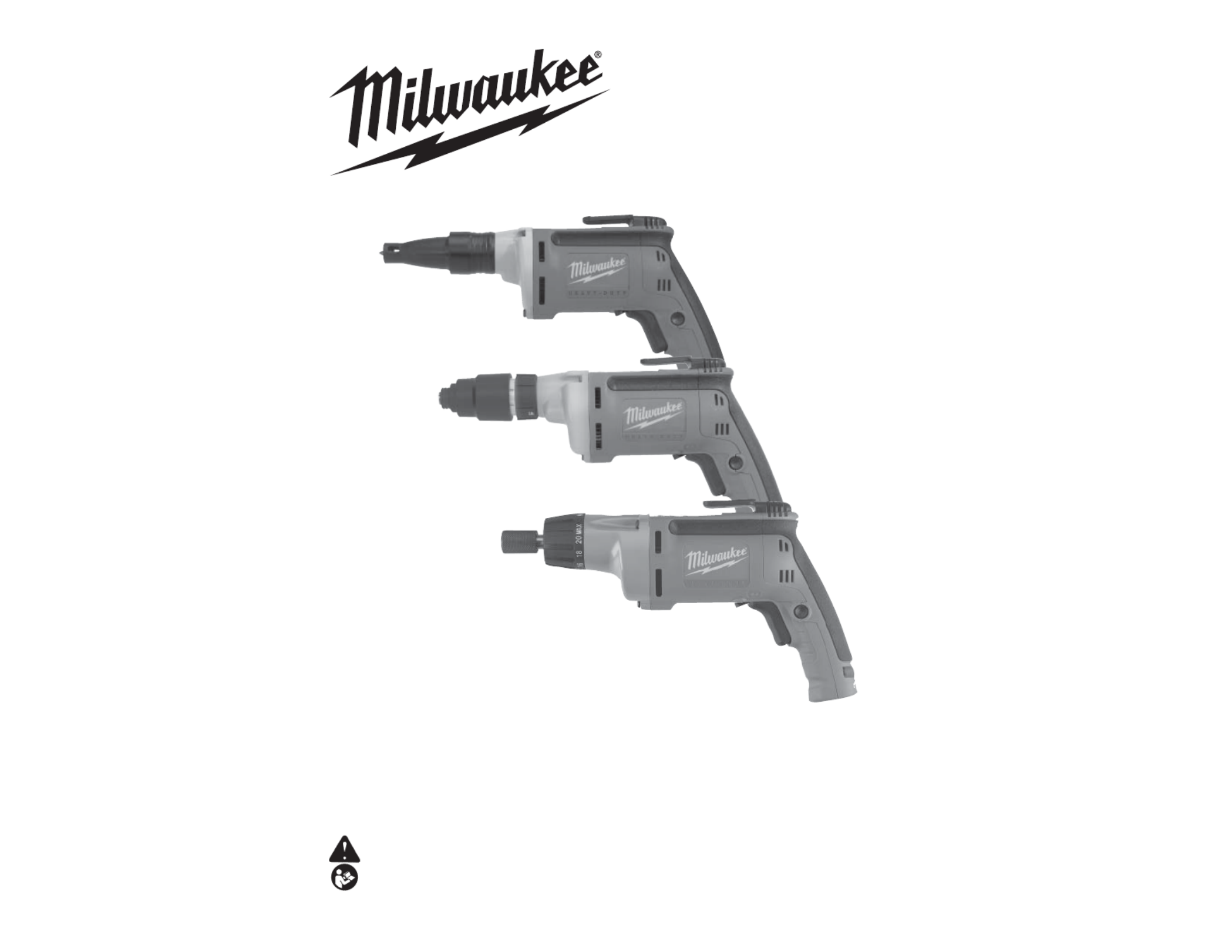
Cat. No. / No de cat.
6580-20, 6740-20, 6742-20, 6780-20,
6790-20, 6791-20, 6791-21, 6792-20
OPERATOR'S MANUAL
MANUEL de L'UTILISATEUR
MANUAL del OPERADOR
WARNING To reduce the risk of injury, user must read and understand operator's manual.
AVERTISSEMENT Afi n de réduire le risque de blessures, l'utilisateur doit lire et bien
comprendre le manuel.
ADVERTENCIA Para reducir el riesgo de lesiones, el usuario debe leer y entender el manual.
HEAVY-DUTY SCREWDRIVER
EXTRA ROBUSTE TOURNEVIS
DESTORNILLADORES HEAVY-DUTY
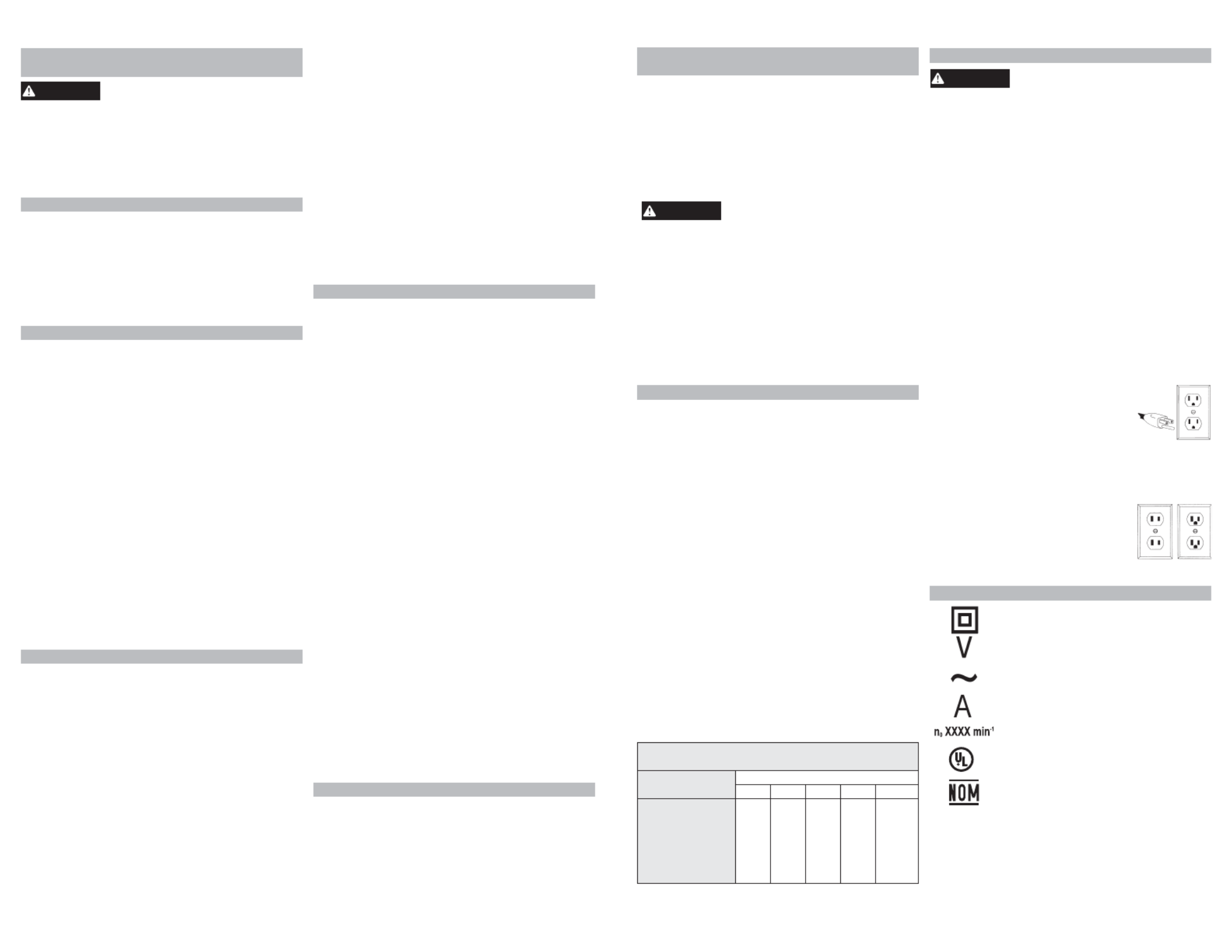
23
GENERAL POWER TOOL
SAFETY WARNINGS
WARNING
Read all safety warnings, instruc-
tions, illustrations and specifi ca-
tions provided with this power tool. Failure to
follow all instructions listed below may result in
electric shock, fi re and/or serious injury. Save all
warnings and instructions for future reference.
The term "power tool" in the warnings refers to your
mains-operated (corded) power tool or battery-oper-
ated (cordless) power tool.
WORK AREA SAFETY
• Keep work area clean and well lit. Cluttered or
dark areas invite accidents.
• Do not operate power tools in explosive atmo-
spheres, such as in the presence of fl ammable
liquids, gases or dust. Power tools create sparks
which may ignite the dust or fumes.
• Keep children and bystanders away while operat-
ing a power tool. Distractions can cause you to lose
control.
ELECTRICAL SAFETY
• Power tool plugs must match the outlet. Never
modify the plug in any way. Do not use any
adapter plugs with earthed (grounded) power
tools. Unmodifi ed plugs and matching outlets will
reduce risk of electric shock.
• Avoid body contact with earthed or grounded
surfaces, such as pipes, radiators, ranges and
refrigerators. There is an increased risk of electric
shock if your body is earthed or grounded.
• Do not expose power tools to rain or wet condi-
tions. Water entering a power tool will increase the
risk of electric shock.
• Do not abuse the cord. Never use the cord for
carrying, pulling or unplugging the power tool.
Keep cord away from heat, oil, sharp edges or
moving parts. Damaged or entangled cords increase
the risk of electric shock.
• When operating a power tool outdoors, use an
extension cord suitable for outdoor use. Use of
a cord suitable for outdoor use reduces the risk of
electric shock.
• If operating a power tool in a damp location is
unavoidable, use a ground fault circuit interrupter
(GFCI) protected supply. Use of an GFCI reduces
the risk of electric shock.
PERSONAL SAFETY
• Stay alert, watch what you are doing and use
common sense when operating a power tool. Do
not use a power tool while you are tired or under
the infl uence of drugs, alcohol or medication. A
moment of inattention while operating power tools
may result in serious personal injury.
• Use personal protective equipment. Always
wear eye protection. Protective equipment such
as a dust mask, non-skid safety shoes, hard hat or
hearing protection used for appropriate conditions
will reduce personal injuries.
• Prevent unintentional starting. Ensure the switch
is in the off-position before connecting to power
source and/or battery pack, picking up or carrying
the tool. Carrying power tools with your fi nger on
the switch or energizing power tools that have the
switch on invites accidents.
• Remove any adjusting key or wrench before
turning the power tool on. A wrench or a key left
attached to a rotating part of the power tool may
result in personal injury.
• Do not overreach. Keep proper footing and
balance at all times. This enables better control
of the power tool in unexpected situations.
• Dress properly. Do not wear loose clothing or
jewelry. Keep your hair and clothing away from
moving parts. Loose clothes, jewelry or long hair
can be caught in moving parts.
• If devices are provided for the connection of
dust extraction and collection facilities, ensure
these are connected and properly used. Use of
dust collection can reduce dust-related hazards.
• Do not let familiarity gained from frequent use
of tools allow you to become complacent and
ignore tool safety principles. A careless action can
cause severe injury within a fraction of a second.
POWER TOOL USE AND CARE
• Do not force the power tool. Use the correct power
tool for your application. The correct power tool
will do the job better and safer at the rate for which
it was designed.
• Do not use the power tool if the switch does not
turn it on and o. Any power tool that cannot be
controlled with the switch is dangerous and must be
repaired.
• Disconnect the plug from the power source and/
or remove the battery pack, if detachable, from
the power tool before making any adjustments,
changing accessories, or storing power tools.
Such preventive safety measures reduce the risk of
starting the power tool accidentally.
• Store idle power tools out of the reach of children
and do not allow persons unfamiliar with the
power tool or these instructions to operate the
power tool. Power tools are dangerous in the hands
of untrained users.
• Maintain power tools and accessories. Check
for misalignment or binding of moving parts,
breakage of parts and any other condition that
may affect the power tool’s operation. If damaged,
have the power tool repaired before use. Many
accidents are caused by poorly maintained power
tools.
• Keep cutting tools sharp and clean. Properly
maintained cutting tools with sharp cutting edges
are less likely to bind and are easier to control.
• Use the power tool, accessories and tool bits
etc. in accordance with these instructions,
taking into account the working conditions and
the work to be performed. Use of the power tool
for operations dierent from those intended could
result in a hazardous situation.
• Keep handles and grasping surfaces dry, clean
and free from oil and grease. Slippery handles and
grasping surfaces do not allow for safe handling and
control of the tool in unexpected situations.
SERVICE
• Have your power tool serviced by a qualifi ed
repair person using only identical replacement
parts. This will ensure that the safety of the power
tool is maintained.
SPECIFIC SAFETY RULES FOR
SCREWDRIVER
• Hold power tool by insulated gripping surfaces,
when performing an operation where the fastener
may contact hidden wiring or its own cord. Fas-
teners contacting a “live” wire may make exposed
metal parts of the power tool “live” and could give
the operator an electric shock.
• Maintain labels and nameplates. These carry
important information. If unreadable or missing,
contact a MILWAUKEE service facility for a free
replacement.
•
WARNING
Some dust created by power sanding,
sawing, grinding, drilling, and other
construction activities contains chemicals known to
cause cancer, birth defects or other reproductive
harm. Some examples of these chemicals are:
• lead from lead-based paint
• crystalline silica from bricks and cement and other
masonry products, and
• arsenic and chromium from chemically-treated lumber.
Your risk from these exposures varies, depending on
how often you do this type of work. To reduce your
exposure to these chemicals: work in a well ventilated
area, and work with approved safety equipment, such
as those dust masks that are specially designed to
fi lter out microscopic particles.
EXTENSION CORDS
Grounded tools require a three wire extension cord.
Double insulated tools can use either a two or three
wire extension cord. As the distance from the supply
outlet increases, you must use a heavier gauge exten-
sion cord. Using extension cords with inadequately
sized wire causes a serious drop in voltage, resulting
in loss of power and possible tool damage. Refer to
the table shown to determine the required minimum
wire size.
The smaller the gauge number of the wire, the greater
the capacity of the cord. For example, a 14 gauge
cord can carry a higher current than a 16 gauge cord.
When using more than one extension cord to make
up the total length, be sure each cord contains at
least the minimum wire size required. If you are using
one extension cord for more than one tool, add the
nameplate amperes and use the sum to determine
the required minimum wire size.
Guidelines for Using Extension Cords
• If you are using an extension cord outdoors, be sure
it is marked with the suffi x “W-A” (“W” in Canada) to
indicate that it is acceptable for outdoor use.
• Be sure your extension cord is properly wired and in
good electrical condition. Always replace a damaged
extension cord or have it repaired by a qualifi ed
person before using it.
• Protect your extension cords from sharp objects,
excessive heat and damp or wet areas.
Recommended Minimum Wire Gauge
For Extension Cords*
Nameplate Amps
Extension Cord Length
25' 50' 75' 100' 150'
0 - 2.0
2.1 - 3.4
3.5 - 5.0
5.1 - 7.0
7.1 - 12.0
12.1 - 16.0
16.1 - 20.0
18
18
18
18
16
14
12
18
18
18
16
14
12
10
18
18
16
14
12
10
--
18
16
14
12
10
--
--
16
14
12
12
--
--
--
* Based on limiting the line voltage drop to fi ve volts at 150%
of the rated amperes.
GROUNDING
WARNING
Improperly connecting the ground-
ing wire can result in the risk of
electric shock. Check with a qualifi ed electrician
if you are in doubt as to whether the outlet is
properly grounded. Do not modify the plug pro-
vided with the tool. Never remove the grounding
prong from the plug. Do not use the tool if the
cord or plug is damaged. If damaged, have it
repaired by a MILWAUKEE service facility before
use. If the plug will not fi t the outlet, have a
proper outlet installed by a qualifi ed electrician.
Grounded Tools (Three-Prong Plugs)
Tools marked “Grounding Required” have a three
wire cord and three prong grounding plug. The plug
must be connected to a properly grounded outlet
(See Figure A). If the tool should electrically mal-
function or break down, grounding provides a low
resistance path to carry electricity away from the
user, reducing the risk of electric shock.
The grounding prong in the plug is connected through
the green wire inside the cord to the grounding
system in the tool. The green wire in the cord must
be the only wire connected to the tool's grounding
system and must never be attached to an electrically
“live” terminal.
Your tool must be plugged into an appro-
Fig. A
priate outlet, properly installed and
grounded in accordance with all codes
and ordinances. The plug and outlet
should look like those in Figure A.
Double Insulated Tools (Two-Prong Plugs)
Tools marked “Double Insulated” do not require
grounding. They have a special double insulation
system which satisfi es OSHA requirements and
complies with the applicable standards
Fig. B Fig. C
of Underwriters Laboratories, Inc., the
Canadian Standard Association and
the National Electrical Code. Double
Insulated tools may be used in either
of the 120 volt outlets shown in Figures
B and C.
SYMBOLOGY
Double Insulated
Volts
Alternating Current
Amps
No Load Revolutions per Minute (RPM)
C US UL Listing for Canada and U.S.
Approval Mark for Mexico
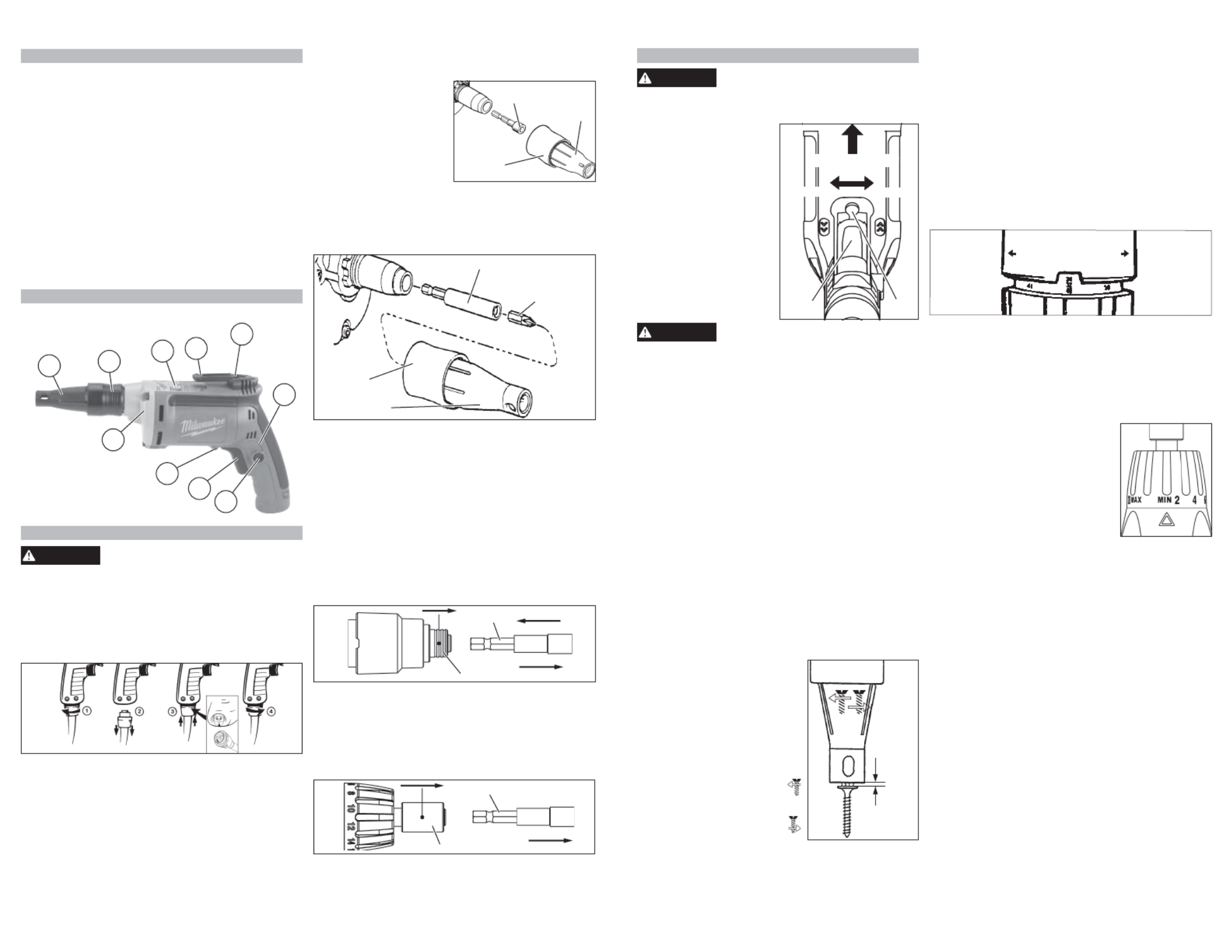
45
Installing and Removing Bits
TEKS Ramp-O Locator Assembly
The locator assembly must
Magnetic socket
Locator
Ramp-o
sleeve
be removed when chang-
ing bit sizes.
1. Unplug tool. To remove
the locator assembly,
t u rn t h e r a m p - o f f
sleeve while pulling it
away from the tool.
2. Pull out the magnetic
socket and replace it with a new socket.
3. Push the locator assembly onto the nose of the
tool until it snaps into place.
Installing and Removing Bits
Drywall Ramp-O Locator Assembly
Bit holder
Insert bit
Locator
Ramp-o
sleeve
1. Unplug tool. To remove the locator assembly, turn
the ramp-o sleeve while pulling it away from the
tool.
2. Push insert bit into bit holder until it snaps into
place. Push the bit holder into the nose of the tool
until it snaps into place.
3. Push the locator assembly onto the nose of the
tool until it snaps into place.
Installing and Removing Magnetic
Sockets on Adjustable Screwdrivers
For Cat. No. 6580-20
1. Unplug tool.
2. To remove the magnetic socket, slide the locking
sleeve forward and pull out the socket.
Locking sleeve
Socket
3. To install the magnetic socket, slide the locking
sleeve forward and push in the socket until it is
fully seated.
For Cat. No. 6780-20
1. Unplug tool.
2. To remove the magnetic socket, slide the locking
sleeve forward and pull out the socket.
Locking sleeve
Socket
3. To install the magnetic socket, simply push in the
socket until it snaps into place.
OPERATION
WARNING
To reduce the risk of injury, always
wear safety goggles or glasses
with side shields.
Using Forward/Reverse Switch
1. For forward (clockwise)
Forward
Trigger
Reverse
Switch
Front of Tool
rotation, push the for-
ward/reverse switch to
the left position as
shown.
2. For reverse (coun-
terclockwise) rotation,
push the forward/re-
verse switch to the right
position as shown.
Although an interlock
prevents reversing the
tool while the motor
is running, allow it to
come to a full stop be-
fore reversing.
WARNING
To reduce the risk of injury, keep
hands and cord away from the bit
and all moving parts.
Starting, Stopping and Controlling Speed
1. To start the tool, pull the trigger.
2. To stop the tool, release the trigger.
3. To vary the drilling speed, simply increase or
decrease pressure on the trigger. The further the
trigger is pulled, the greater the speed.
Locking Trigger
The lock button holds the trigger in the ON position
for continuous full speed use.
1. To lock the trigger, hold the lock button in while
pulling the trigger. Release the trigger.
2. To unlock the trigger, pull the trigger and release.
The lock button will pop out.
Adjusting Locator Assembly
The locator assembly controls the tool's driving
depth. These screwdrivers feature a locator assembly
with one-handed depth adjustment. Depth adjust-
ments can be made easily and quickly by turning
the locator with one hand. Detents inside the sleeve
“lock” the selected depth.
For the drywall ramp-o locator assembly, start with
about 1/16" clearance between the head of the screw
and nose with the snap-action clutch disengaged
as shown.
For both locator assemblies, the
1/16"
detents on the inside of the
sleeve represent different
depths. Every two clicks of the
locator equal 1/64". Continue
adjusting the locator to the
desired depth.
1. To increase the driving
depth, simply rotate the loca-
tor in the direction labeled .
2. To decrease the driving
depth, simply rotate the loca-
tor in the direction labeled .
The detents “lock” the locator
in place, ensuring an accurate depth setting.
3. To remove the locator assembly, turn the ramp-o
sleeve while pulling it away from the tool. Reat-
taching the locator assembly will not change the
depth setting.
SPECIFICATIONS
Volts .............................................................120 AC
Amps ..................................................................6.5
Cat. No. ..................................................... 6580-20
RPM ............................................................ 0 -1200
Cat. No. ..................................................... 6740-20
RPM ........................................................... 0 - 2500
Cat. No. ..................................................... 6742-20
RPM ........................................................... 0 - 4300
Cat. No. ..................................................... 6780-20
RPM ........................................................... 0 - 2900
Cat. No. ..................................................... 6790-20
RPM ........................................................... 0 - 2500
Cat. No. ..................................................... 6791-20
RPM ........................................................... 0 - 2500
Cat. No. ..................................................... 6791-20
RPM ........................................................... 0 - 2500
Cat. No. ..................................................... 6792-20
RPM ........................................................... 0 - 2500
FUNCTIONAL DESCRIPTION
1234
7
1. Locator
2. Ramp-o sleeve
3. Nameplate
8
9
10
4. Belt clip
5. Bit clip
6. Handle
7. Lock button
8. Trigger
9. Forward/Reverse switch
10. Gear case
6
5
ASSEMBLY
WARNING
To reduce the risk of injury, always
unplug tool before changing or
removing accessories. Only use accessories
specifi cally recommended for this tool. Others
may be hazardous.
Removing and Replacing Quik-Lok® Cords
(Cat. No. 6580-20, 6791-20)
MILWAUKEE's exclusive Quik-Lok
® Cords provide
instant fi eld replacement or substitution.
1. To remove the Quik-Lok® Cord, turn the cord nut
1/4 turn to the left and pull it out.
2. To replace the Quik-Lok
® Cord, align the connector
keyways and push the connector in as far as it will
go. Turn the cord nut 1/4 turn to the right to lock.
Adjusting Torque Setting
These screwdrivers have a torque setting adjustment
collar for driving different types of screws into different
materials. When properly adjusted, the clutch will slip
at a preset torque to prevent driving the screw too
deep and to prevent damage to the screw or tool.
For Cat. Nos. 6580-20
The 6580-20 Screwdriver has a torque setting adjust-
ment collar that may be adjusted to one of forty-four
settings. The torque is adjustable from 10 to 140
inch-pounds.
To select a setting, turn the adjustment collar in the
direction indicated on the tool. The selected setting
will appear in the window as shown.
HIGHER -TORQUE - LOWER
SETTING
NOTE: Use a piece of scrap material to test the dif-
ferent settings before driving screws into workpiece.
To determine a specifi c setting for your application,
use a torque wrench to check the correct torque at
any particular setting.
For Cat. No. 6780-20
The 6780-20 Screwdriver has a torque setting adjust-
ment collar that may be adjusted to one of twenty-one
settings. The torque is adjustable
from 10 to 140 inch-pounds.
To select a setting, turn the ad-
justment collar on the tool. The
selected setting will appear above
the arrow as shown.
NOTE: Use a piece of scrap mate-
rial to test the dierent settings be-
fore driving screws into workpiece.
To determine a specifi c setting for your application,
use a torque wrench to check the correct torque at
any particular setting.
Product specificaties
Merk: | Milwaukee |
Categorie: | Schroefmachine |
Model: | 6742-20 |
Heb je hulp nodig?
Als je hulp nodig hebt met Milwaukee 6742-20 stel dan hieronder een vraag en andere gebruikers zullen je antwoorden
Handleiding Schroefmachine Milwaukee
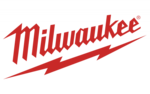
31 Maart 2025
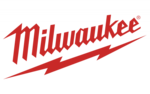
20 November 2024
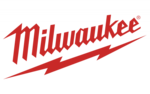
16 November 2024
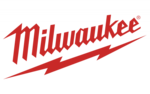
16 November 2024
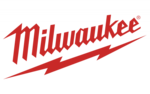
4 September 2024
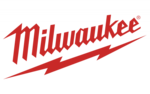
23 Juni 2024
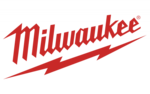
10 Juni 2024
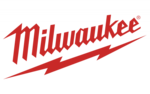
5 Mei 2024
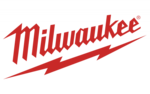
10 April 2024
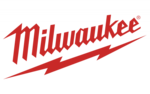
10 April 2024
Handleiding Schroefmachine
- Schroefmachine Bosch
- Schroefmachine Panasonic
- Schroefmachine AEG
- Schroefmachine DeWalt
- Schroefmachine Basetech
- Schroefmachine Batavia
- Schroefmachine Bavaria
- Schroefmachine Black Decker
- Schroefmachine Bruder Mannesmann
- Schroefmachine Dremel
- Schroefmachine Easymaxx
- Schroefmachine Einhell
- Schroefmachine Elu
- Schroefmachine Fein
- Schroefmachine Ferm
- Schroefmachine Festool
- Schroefmachine Fuxtec
- Schroefmachine Goon
- Schroefmachine Greenworks
- Schroefmachine Gude
- Schroefmachine Hikoki
- Schroefmachine Hitachi
- Schroefmachine Ingersoll Rand
- Schroefmachine Kawasaki
- Schroefmachine Kress
- Schroefmachine Laserliner
- Schroefmachine Makita
- Schroefmachine Maktec
- Schroefmachine Matrix
- Schroefmachine Metabo
- Schroefmachine Parkside
- Schroefmachine Powerfix
- Schroefmachine Powerplus
- Schroefmachine Ryobi
- Schroefmachine Silverline
- Schroefmachine Skil
- Schroefmachine Stanley
- Schroefmachine Toolcraft
- Schroefmachine Toolland
- Schroefmachine Trotec
- Schroefmachine Velleman
- Schroefmachine Vonroc
- Schroefmachine Westfalia
- Schroefmachine Wiha
- Schroefmachine Worx
- Schroefmachine Omega
- Schroefmachine Ozito
- Schroefmachine Black And Decker
- Schroefmachine Steren
- Schroefmachine Urrea
- Schroefmachine Cocraft
- Schroefmachine Meec Tools
- Schroefmachine Senco
- Schroefmachine Genesis
- Schroefmachine Hilti
- Schroefmachine Facom
- Schroefmachine Kraftwerk
- Schroefmachine EMOS
- Schroefmachine Cotech
- Schroefmachine Power Craft
- Schroefmachine Tacklife
- Schroefmachine Truper
- Schroefmachine Fieldmann
- Schroefmachine Mafell
- Schroefmachine Carrera
- Schroefmachine Biltema
- Schroefmachine Porter-Cable
- Schroefmachine Beta
- Schroefmachine Dedra
- Schroefmachine MSW
- Schroefmachine Sthor
- Schroefmachine Craftsman
- Schroefmachine Chamberlain
- Schroefmachine Chicago Pneumatic
- Schroefmachine Alpha Tools
- Schroefmachine Hazet
- Schroefmachine Yato
- Schroefmachine Total
- Schroefmachine Abac
- Schroefmachine Meister Craft
- Schroefmachine StarTech.com
- Schroefmachine Park Tool
- Schroefmachine Pansam
- Schroefmachine Gedore
- Schroefmachine Netter Vibration
- Schroefmachine NEO Tools
- Schroefmachine SW-Stahl
- Schroefmachine Cleco
- Schroefmachine Einhell Bavaria
- Schroefmachine Prowork
- Schroefmachine Proviel
- Schroefmachine Weidmüller
- Schroefmachine Mac Tools
- Schroefmachine Wera
- Schroefmachine Rodcraft
- Schroefmachine Bavaria By Einhell
- Schroefmachine TAURUS Titanium
Nieuwste handleidingen voor Schroefmachine

31 Maart 2025

31 Maart 2025

30 Maart 2025

29 Maart 2025

29 Maart 2025

28 Maart 2025

28 Maart 2025

28 Maart 2025

28 Maart 2025

28 Maart 2025