Juki DDL-8000A Handleiding
Juki
Naaimachine
DDL-8000A
Lees hieronder de 📖 handleiding in het Nederlandse voor Juki DDL-8000A (68 pagina's) in de categorie Naaimachine. Deze handleiding was nuttig voor 76 personen en werd door 2 gebruikers gemiddeld met 4.5 sterren beoordeeld
Pagina 1/68
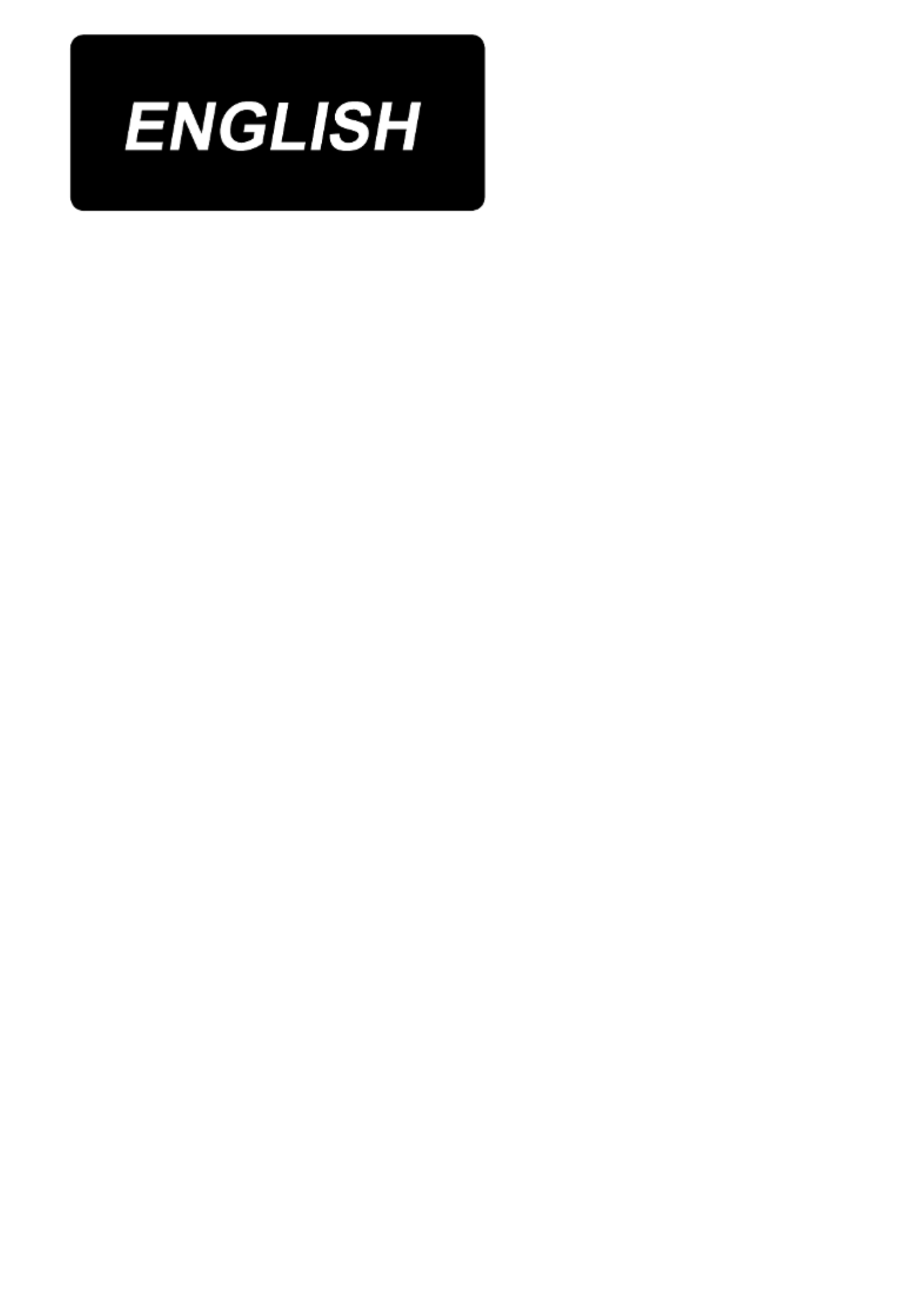
DDL-8000A
INSTRUCTION MANUAL
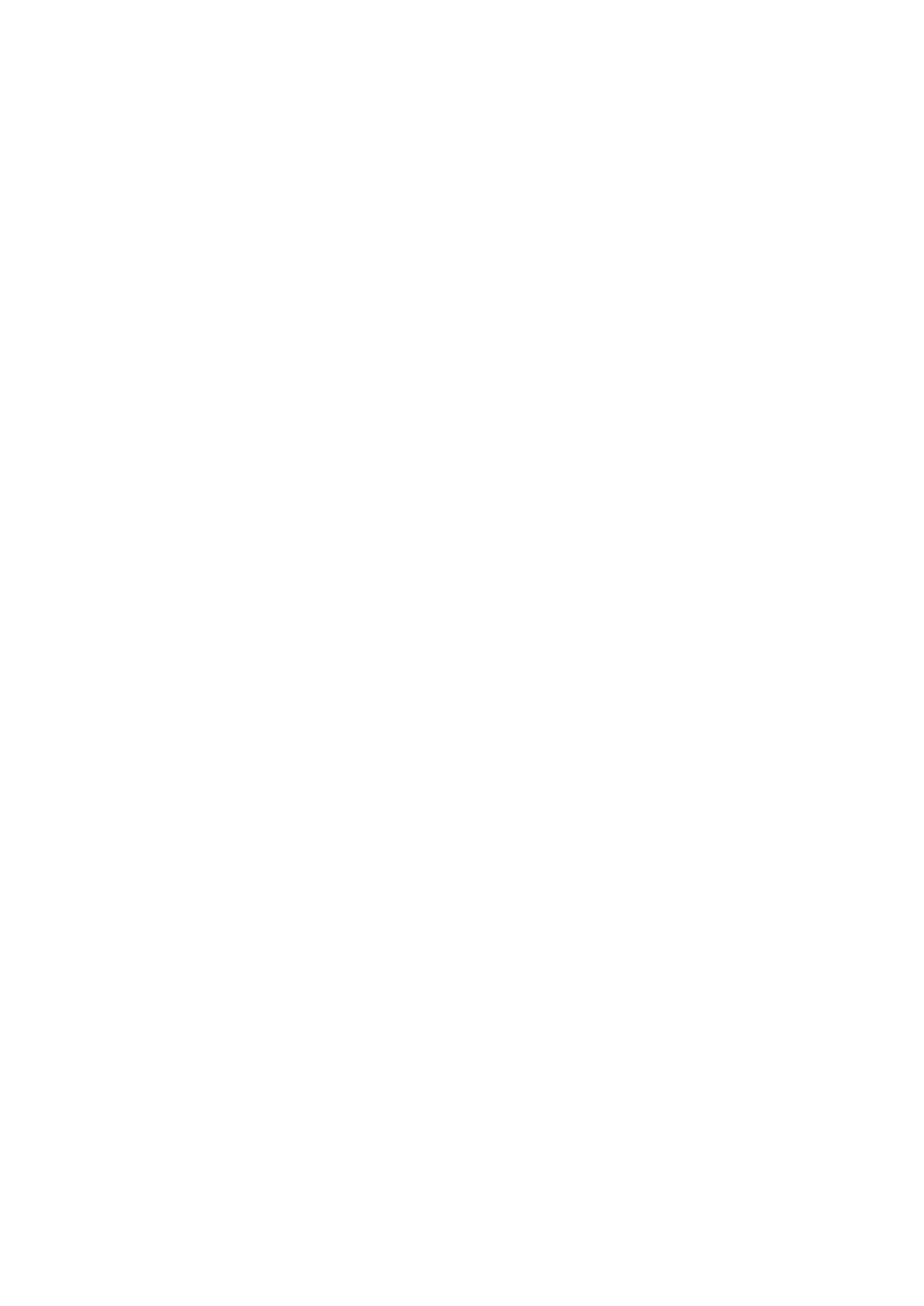
CONTENTS
1. SPECIFICATIONS 1 ............................................................................................................
1-1. Specications of the sewing machine head ..................................................................... 1
1-2. Specications of the control box ....................................................................................... 1
2. SET UP 2 .............................................................................................................................
2-1. Drawing of table ................................................................................................................... 2
2-2. Cautions when setting up the sewing machine ................................................................ 3
2-2-1. How to carry the sewing machine ............................................................................................ 3
2-2-2. Caution when placing the sewing machine ............................................................................. 3
2-3. Installation ............................................................................................................................ 3
2-4. Installing the pedal sensor ................................................................................................. 4
2-5. Connecting the connector .................................................................................................. 5
2-6. Installing the power switch (for CE) .................................................................................. 6
2-7. Installing the reactor box .................................................................................................... 7
2-8. How to install the power plug ............................................................................................. 8
2-9. Installing the thread stand .................................................................................................. 9
2-10. Attaching the connecting rod ............................................................................................. 9
2-11. Adjustment of the pedal .................................................................................................... 10
2-11-1. Installing the connecting rod ................................................................................................10
2-11-2. Adjusting the pedal angle...................................................................................................... 10
2-12. Pedal operation .................................................................................................................. 10
2-13. Power switch ...................................................................................................................... 11
2-14. Lubrication ......................................................................................................................... 12
3. PREPARATION BEFORE SEWING 13 ..............................................................................
3-1. Attaching the needle ......................................................................................................... 13
3-2. Removing/tting the bobbin case .................................................................................... 13
3-3. Winding the bobbin thread ............................................................................................... 14
3-4. Threading the machine head ............................................................................................ 15
3-5. Thread tension ................................................................................................................... 15
3-5-1. Adjusting the needle thread tension ...................................................................................... 15
3-5-2. Adjusting the bobbin thread tension .....................................................................................15
3-6. Presser foot pressure ....................................................................................................... 16
3-7. Adjusting the stitch length ............................................................................................... 16
3-8. Changing the sewing speed ............................................................................................. 17
3-9. LED hand light ................................................................................................................... 18
3-10. Reverse feed stitching ...................................................................................................... 18
3-11. Adjusting the amount of oil (oil splashes) in the hook .................................................. 19
3-11-1. Adjusting the amount of oil in the hook............................................................................... 19
3-11-2. How to conrm the amount of oil (oil splashes) ................................................................. 20
3-11-3. Sample showing the appropriate amount of oil .................................................................. 20
3-12. Adjusting the thread take-up spring and the thread take-up stroke............................. 21
4. FOR THE OPERATOR 22 ...................................................................................................
4-1. How to set the machine head and to initialize data (the factory-set state at the time
of shipment) ....................................................................................................................... 22
i
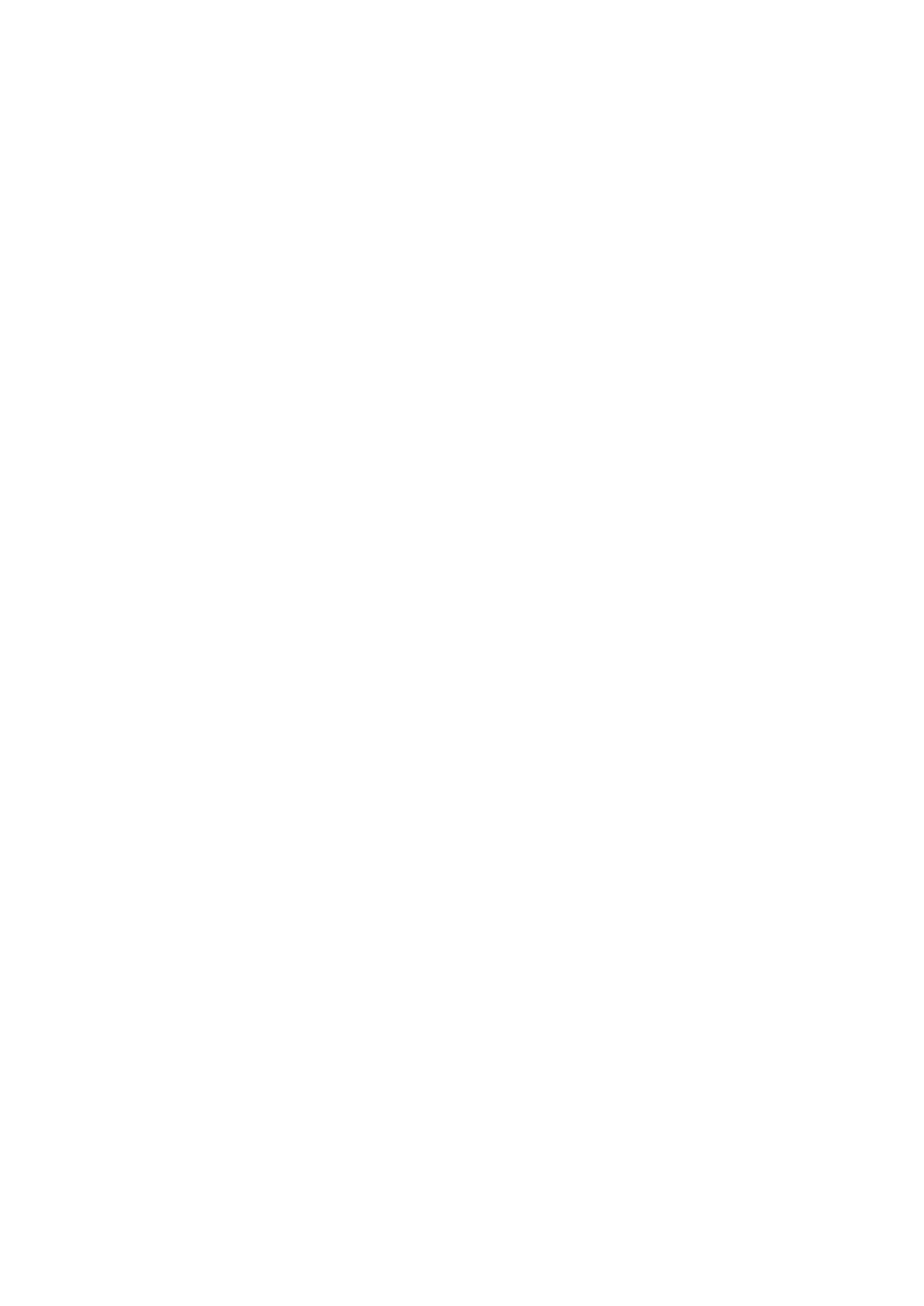
4-2. Operation panel ................................................................................................................. 23
4-3. Audio guidance .................................................................................................................. 25
4-4. Setting the clock ................................................................................................................ 26
4-5. Operating procedure of the sewing pattern .................................................................... 27
4-5-1. Reverse feed stitching pattern ............................................................................................... 27
4-5-2. Overlapped stitching pattern .................................................................................................. 28
4-5-3. Polygonal-shape stitching pattern ......................................................................................... 29
4-6. Function setting ................................................................................................................. 31
4-7. Setting the function keys (F1 and F2) .............................................................................. 32
4-8. Production support function ............................................................................................ 33
4-8-1. How to set the production support parameters .................................................................... 33
4-8-2. List of production support parameters .................................................................................. 34
4-8-3. How to display the operation rate of the sewing machine ................................................... 35
4-8-4. How to display the number of pieces produced ................................................................... 36
4-9. Function setting list .......................................................................................................... 37
4-10. Detailed explanation of selection of functions ............................................................... 42
4-11. How to use the bobbin counter ........................................................................................ 48
4-12. Initialization of function setting data ............................................................................... 49
4-13. Password lock ................................................................................................................... 50
4-14. About the USB ................................................................................................................... 51
5. ADJUSTMENT OF THE MACHINE HEAD (APPLICATION) ........................................ 52
5-1. Needle-to-hook relationship ............................................................................................. 52
5-2. Adjusting the needle thread presser device ................................................................... 53
5-3. Adjusting the thread trimmer ........................................................................................... 56
5-3-1. For checking of the thread trimming cam timing ................................................................. 56
5-3-2. Adjustment of the thread trimming cam timing .................................................................... 56
5-3-3. Checking of the knife unit ....................................................................................................... 57
5-3-4. Adjustment of the knife unit.................................................................................................... 58
5-4. Adjusting the main shaft stop position ........................................................................... 59
5-5. Grease shortage warning ................................................................................................. 60
5-5-1. Grease shortage warning ........................................................................................................ 60
5-5-2. Grease shortage error ............................................................................................................. 60
5-5-3. How to reset the grease shortage error ................................................................................. 61
5-6. Disposal of batteries ......................................................................................................... 62
6. CARE 63 .............................................................................................................................
6-1. Cleaning ............................................................................................................................. 63
6-2. Applying grease ................................................................................................................. 64
6-3. Applying grease to the needle bar lower bushing .......................................................... 64
7. LIST OF ERROR CODES 65 ..............................................................................................
ii
Product specificaties
Merk: | Juki |
Categorie: | Naaimachine |
Model: | DDL-8000A |
Heb je hulp nodig?
Als je hulp nodig hebt met Juki DDL-8000A stel dan hieronder een vraag en andere gebruikers zullen je antwoorden
Handleiding Naaimachine Juki

16 November 2024

16 November 2024

16 November 2024

19 Maart 2024

6 Januari 2024

5 Januari 2024

5 Januari 2024

5 Januari 2024

1 December 2023

22 Maart 2023
Handleiding Naaimachine
- Naaimachine IKEA
- Naaimachine AEG
- Naaimachine Medion
- Naaimachine Siemens
- Naaimachine Aigger
- Naaimachine Alfa
- Naaimachine Ambiano
- Naaimachine Anker-Bernette
- Naaimachine Baby Lock
- Naaimachine Bernina
- Naaimachine Bestron
- Naaimachine Blaupunkt
- Naaimachine Brother
- Naaimachine Durabase
- Naaimachine Durkopp Adler
- Naaimachine Easy Home
- Naaimachine Easymaxx
- Naaimachine Elna
- Naaimachine Emerio
- Naaimachine Empisal
- Naaimachine ER
- Naaimachine Feiyue
- Naaimachine Gritzner
- Naaimachine Hema
- Naaimachine Hofmann
- Naaimachine Home Electric
- Naaimachine Huskystar
- Naaimachine Husqvarna
- Naaimachine Husqvarna-Viking
- Naaimachine Kayser
- Naaimachine Kenmore
- Naaimachine Kohler
- Naaimachine Lervia
- Naaimachine Lewenstein
- Naaimachine Lifetec
- Naaimachine Livoo
- Naaimachine Mediashop
- Naaimachine Micromaxx
- Naaimachine Mio Star
- Naaimachine Muller
- Naaimachine Necchi
- Naaimachine Novamatic
- Naaimachine Pfaff
- Naaimachine Primera
- Naaimachine Privileg
- Naaimachine Siemssen
- Naaimachine Silver
- Naaimachine Silvercrest
- Naaimachine Singer
- Naaimachine Sinojo
- Naaimachine Solac
- Naaimachine Termozeta
- Naaimachine Tesco
- Naaimachine Toyota
- Naaimachine Tristar
- Naaimachine Vendomatic
- Naaimachine Veritas
- Naaimachine Victoria
- Naaimachine W6
- Naaimachine Weasy
- Naaimachine Yamata
- Naaimachine Zippy
- Naaimachine Janome
- Naaimachine Jata
- Naaimachine Jocca
- Naaimachine Crofton
- Naaimachine Guzzanti
- Naaimachine Mellerware
- Naaimachine Sinbo
- Naaimachine Carina
- Naaimachine Kunft
- Naaimachine Prince
- Naaimachine RCE
- Naaimachine Yamato
- Naaimachine Prixton
- Naaimachine Bernette
- Naaimachine Union Special
- Naaimachine Meister Craft
- Naaimachine Łucznik
- Naaimachine LERAN
- Naaimachine SteamMax
Nieuwste handleidingen voor Naaimachine

4 Maart 2025

24 Februari 2025

24 Februari 2025

24 Februari 2025

24 Februari 2025
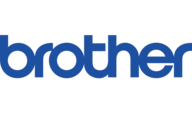
11 Februari 2025
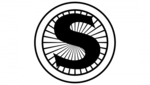
5 Februari 2025

5 Februari 2025
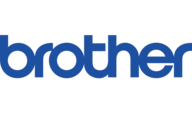
13 Januari 2025
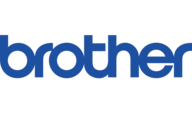
13 Januari 2025