Microchip ATmega32U2 Handleiding
Microchip
Niet gecategoriseerd
ATmega32U2
Bekijk gratis de handleiding van Microchip ATmega32U2 (12 pagina’s), behorend tot de categorie Niet gecategoriseerd. Deze gids werd als nuttig beoordeeld door 32 mensen en kreeg gemiddeld 4.8 sterren uit 16.5 reviews. Heb je een vraag over Microchip ATmega32U2 of wil je andere gebruikers van dit product iets vragen? Stel een vraag
Pagina 1/12
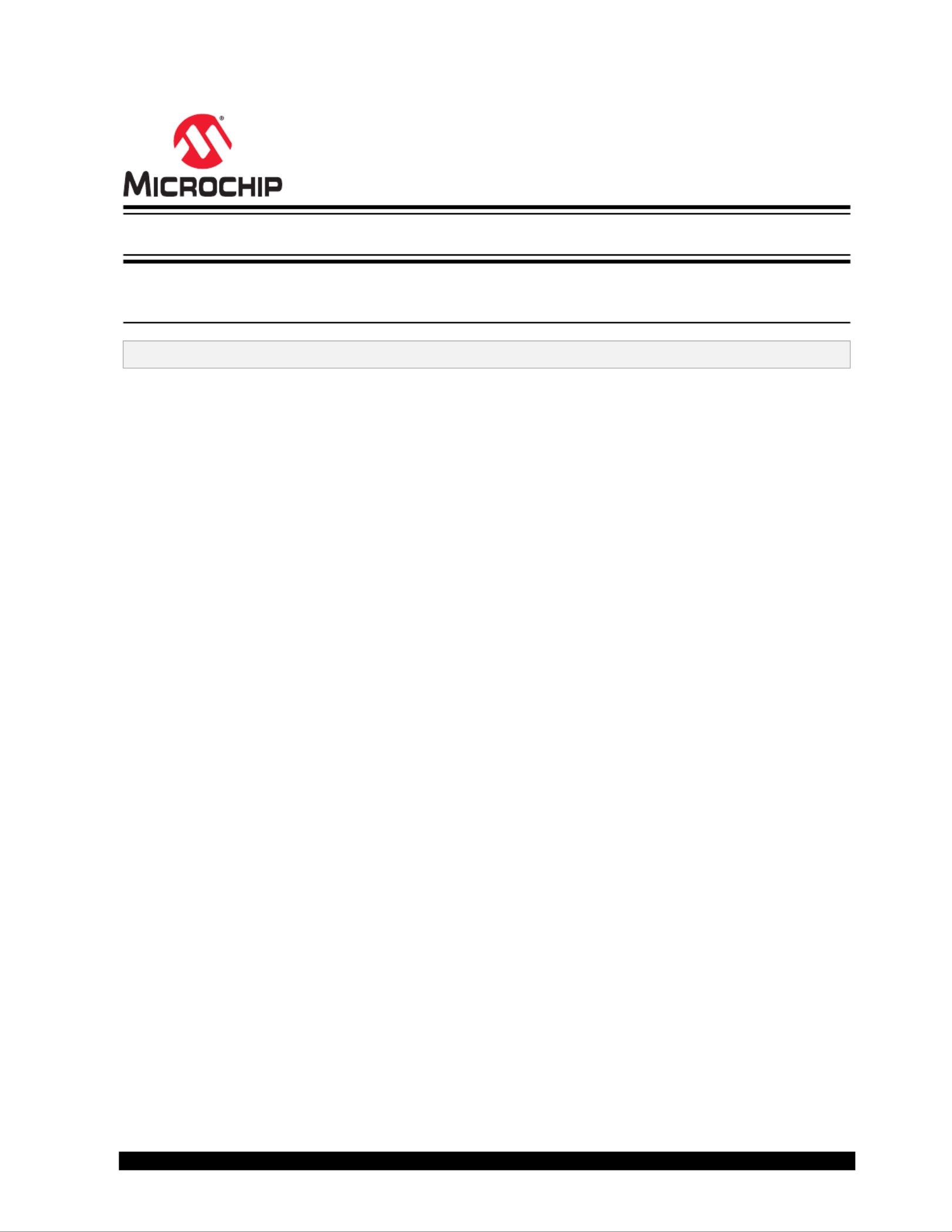
Differential and Single-Ended
ADC
Differential and Single-Ended ADC
Introduction
Author: Kristian Saxrud Bekken, Microchip Technology Inc.
A common requirement for microcontroller applications is the need to sense the real world in one way or another.
This requires bridging the gap between the digital dimension of a microcontroller and the analog realm of the real
world. In most cases, this is accomplished by using a sensor that translates the magnitude of a physical phenomenon
to an analog voltage which is routed to a pin on the microcontroller. Lastly, a dedicated part of the microcontroller
called an analog-to-digital converter, also referred to as an ADC or A/D converter, transforms the analog voltage to a
digital value to be further processed by the microcontroller.
Most analog sensors either output their measured value as a single analog voltage signal or as a difference between
two analog voltage signals. The two concepts are referred to as single-ended signaling and differential signaling,
respectively.
This white paper provides a high-level introduction to A/D conversion of single-ended and differential analog signals
by presenting the main advantages and drawbacks for the two approaches, as well as a selection of common
applications and useful considerations.
© 2019 Microchip Technology Inc. White Paper DS-00003197A-page 1
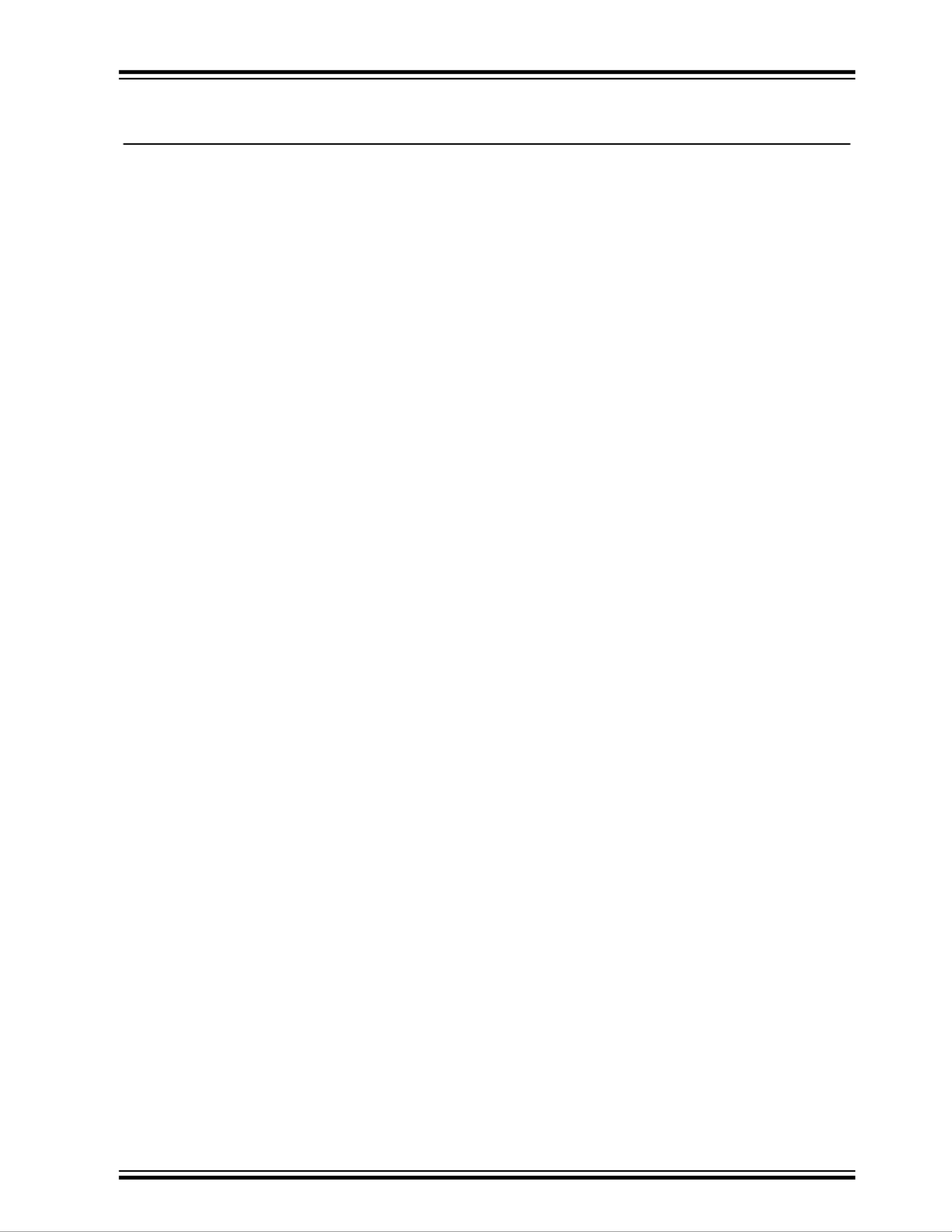
Table of Contents
Introduction.....................................................................................................................................................1
1. Single-Ended Operation..........................................................................................................................3
1.1. General Concept.......................................................................................................................... 3
1.2. Advantages and Drawbacks.........................................................................................................3
1.3. Typical Applications......................................................................................................................3
2. Differential Operation.............................................................................................................................. 5
2.1. General Concept.......................................................................................................................... 5
2.2. Advantages and Drawbacks.........................................................................................................6
2.3. Typical Applications......................................................................................................................6
3. Considerations........................................................................................................................................ 7
4. Revision History...................................................................................................................................... 8
The Microchip Website...................................................................................................................................9
Product Change Notification Service..............................................................................................................9
Customer Support.......................................................................................................................................... 9
Product Identification System.......................................................................................................................10
Microchip Devices Code Protection Feature................................................................................................ 10
Legal Notice................................................................................................................................................. 10
Trademarks.................................................................................................................................................. 10
Quality Management System....................................................................................................................... 11
Worldwide Sales and Service.......................................................................................................................12
Differential and Single-Ended ADC
© 2019 Microchip Technology Inc. White Paper DS-00003197A-page 2
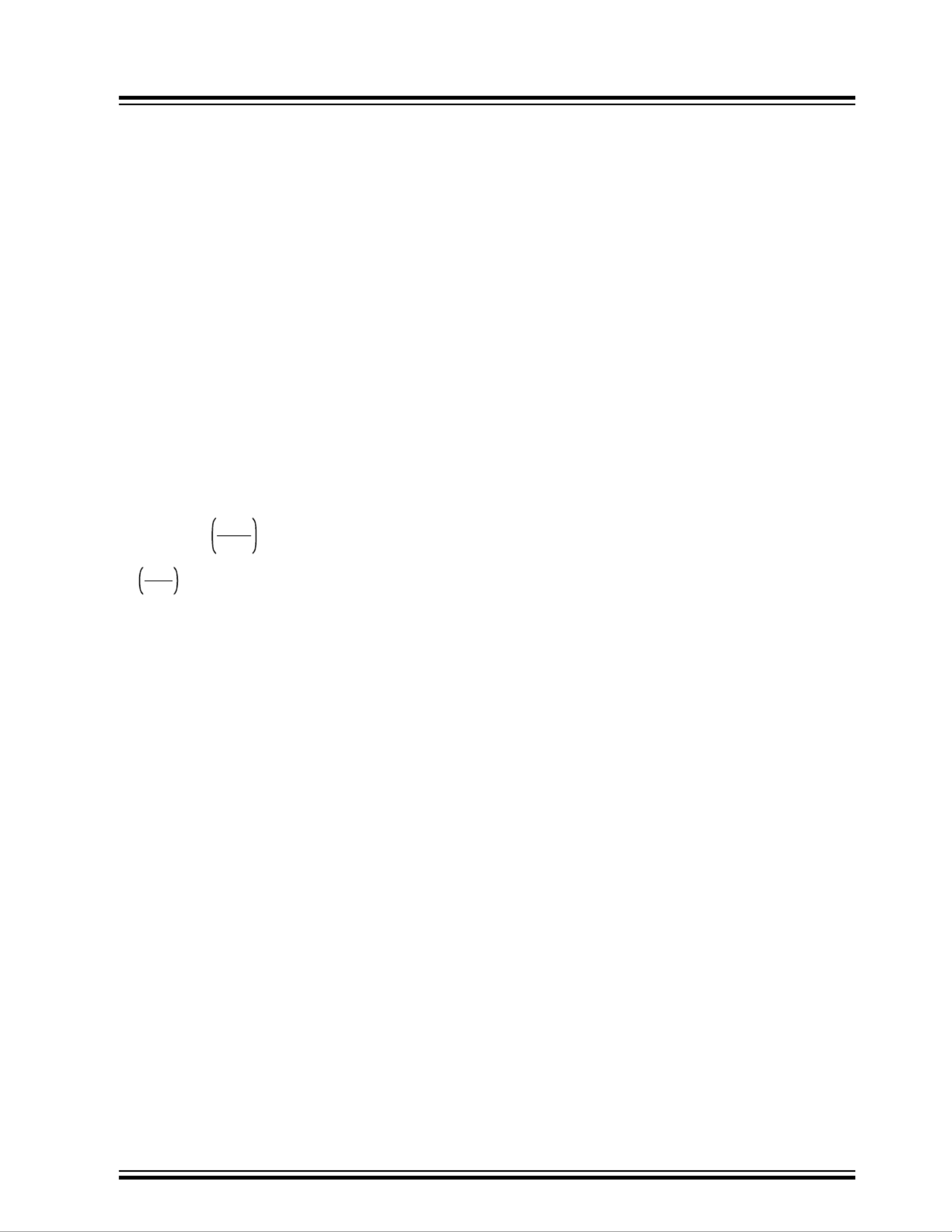
1. Single-Ended Operation
1.1 General Concept
The simplest and most widely used analog sensors provide single-ended signals. These are designed to be
connected to the same ground level as the microcontroller and to provide their measurement result as an analog
voltage signal on a single wire referenced to this common ground. All basic ADCs support single-ended operation.
An ADC can be designed to operate in different ways, and the amount of time required to perform an analog-to-digital
conversion will vary between ADCs. Regardless, the result is a digital representation of the analog input value. The
digital value will typically be an integer between and 0 2
n-1 n, where is the resolution of the ADC in bits. An integer
value of means that the analog voltage level is the same as ground, while the maximum value (0 2
n-1) corresponds
to the level of what is referred to as the ADC voltage reference (V
ref). The voltage reference defines the conversion
range of the ADC, which for single-ended operation means that an analog input above this level still produces the
maximum digital value, while an input below ground level gives a digital value of . In most cases, the ADC voltage0
reference can be selected among different levels between ground and the microcontroller supply voltage in order to
utilize as much of the ADC resolution as possible for inputs in a given voltage range.
A 12-bit single-ended ADC will most likely have an output range of . If the selected [0,4095] V
ref is 2.0V, and the
analog input signal is 0.5V, the corresponding digital value can be calculated as follows:
Equation 1-1. Example - 12-bit Single-Ended Conversion
ADC Output = Input
Total ADC Counts
=0.5V
2.0V 4096
= 1024
1.2 Advantages and Drawbacks
Whether single-ended operation is the best choice in a given setting depends on the specific application. Below are
some of the main advantages and drawbacks associated with this approach.
Main advantages:
• Both sensors and microcontrollers are available at very low cost
• Occupies only one analog microcontroller input per sensor
• In most cases conceptually simple and easy to use
• Large selection of available sensors and microcontrollers
Main drawbacks:
• Sensitive to noise along the analog signal path
• Sensitive to common-mode noise on the ground and reference voltage levels of the microcontroller
• The signal path between the sensor and the microcontroller should be as short as possible to minimize noise
and ground-level differences
• Conditioning circuitry that adds cost and unwanted dynamic effects might be needed
1.3 Typical Applications
There are numerous types of single-ended analog sensors available. Some of the most common use-cases in
microcontroller applications are:
• Potentiometers for measuring angle or position
• Light intensity measurement
• Infrared and ultrasonic range measurement
Differential and Single-Ended ADC
Single-Ended Operation
© 2019 Microchip Technology Inc. White Paper DS-00003197A-page 3
Product specificaties
Merk: | Microchip |
Categorie: | Niet gecategoriseerd |
Model: | ATmega32U2 |
Heb je hulp nodig?
Als je hulp nodig hebt met Microchip ATmega32U2 stel dan hieronder een vraag en andere gebruikers zullen je antwoorden
Handleiding Niet gecategoriseerd Microchip
14 Mei 2025
6 Mei 2025
6 Mei 2025
6 Mei 2025
6 Mei 2025
6 Mei 2025
6 Mei 2025
6 Mei 2025
6 Mei 2025
6 Mei 2025
Handleiding Niet gecategoriseerd
- Crane
- Indesit
- Infinity
- Arturia
- SEH
- Volkswagen
- Gamesir
- Lec
- Ledvance
- Audix
- Craftsman
- FSP/Fortron
- Scancool
- Premium Levella
- Analog Way
Nieuwste handleidingen voor Niet gecategoriseerd
5 Juli 2025
5 Juli 2025
5 Juli 2025
5 Juli 2025
5 Juli 2025
5 Juli 2025
5 Juli 2025
5 Juli 2025
5 Juli 2025